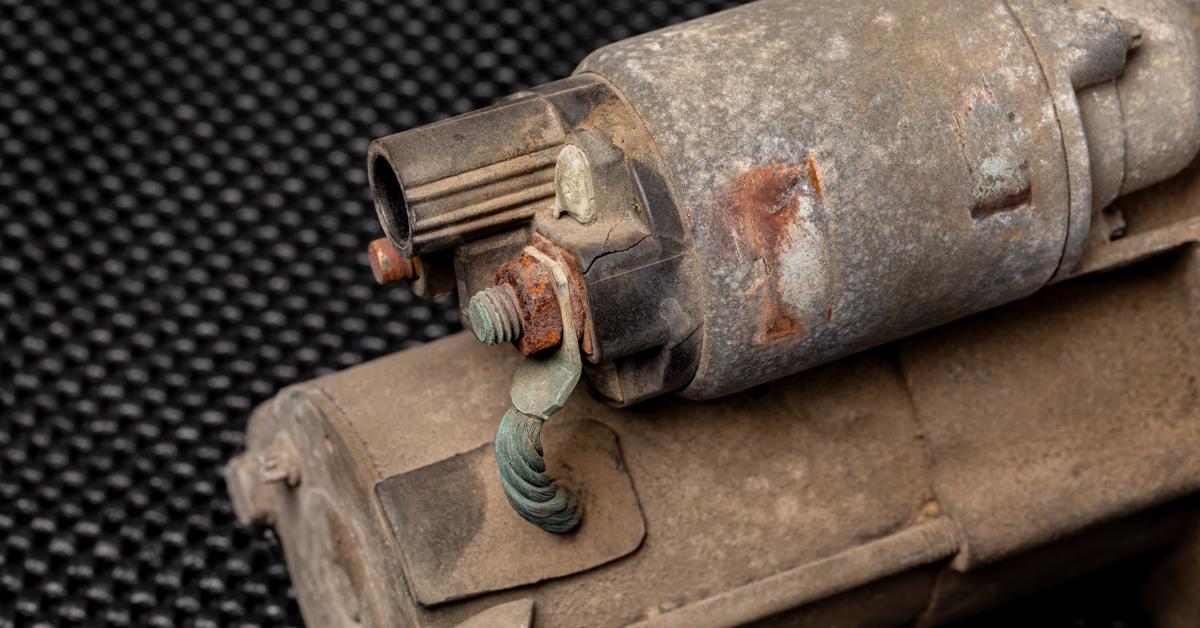
Corrosive environments take a toll on equipment, especially solenoid valves. Harsh chemicals, extreme temperatures, and aggressive fluids can quickly cause leaks, failures, and unplanned downtime. You need to focus on material compatibility and smart design features to support your equipment. This post explains what to know about solenoid valves in corrosive environments so your systems stay reliable and efficient.
What Defines a Corrosive Environment?
A corrosive environment exposes materials to substances that may cause chemical reactions or physical wear. Results include degrading the material’s structure, compromising performance, and failing equipment. Common examples of corrosive environments involve chemical processing plants, marine locations with saltwater exposure, and systems handling strong acids or bases.
Corrosion takes many forms and presents unique challenges. Chemical corrosion occurs when materials react with acids, alkalis, or solvents, breaking down their integrity. Galvanic corrosion arises in systems where dissimilar metals contact and react in an electrolyte, accelerating wear on the anodic material.
Localized issues, such as pitting corrosion, create small but deep holes in metal surfaces, which can compromise functionality if you ignore them. For example, stainless steel valves in seawater suffer from pitting due to chloride exposure.
Why Corrosion Negatively Impacts Solenoid Valves
Corrosion weakens structural components and leads to inefficient or unsafe operations. When a solenoid valve handles abrasive or chemically aggressive media without adequate resistance, its internal components may degrade rapidly.
For instance, in a sulfuric acid handling system, valve material with poor chemical resistance deteriorates quickly, leading to leaks or blockages. Each failure adds downtime, repair costs, and risks of system-wide interruptions.
The Role of Material in Valve Performance
The material composition of a solenoid valve determines its resilience against environmental challenges. Standard materials, such as brass or aluminum, perform adequately in less aggressive applications but fail in settings with aggressive chemicals or erosive substances. Correct material selection ensures the valve operates reliably and minimizes risks associated with corrosion-induced failures.
Stainless Steel and Its Limitations
Stainless steel is one of the most commonly used materials for solenoid valves due to its strength, affordability, and corrosion resistance in moderate environments. However, exposure to strong chlorides, such as seawater or cleaning agents in food processing, can break down its chromium oxide layer and cause damage. High temperatures or acids further compromise its durability, making it unsuitable for certain industrial applications without protection.
Superior Corrosion-Resistant Alloys
Hastelloy and Monel offer the best protection for solenoid valves in corrosive environments. These superalloys resist chemicals, making them suitable for applications involving sulfuric or hydrochloric acid.
Similarly, titanium offers remarkable strength and corrosion resistance when handling seawater or chlorine gases. Although these options have higher upfront costs than standard materials, they extend the valve’s lifespan and lower replacement and maintenance expenses.
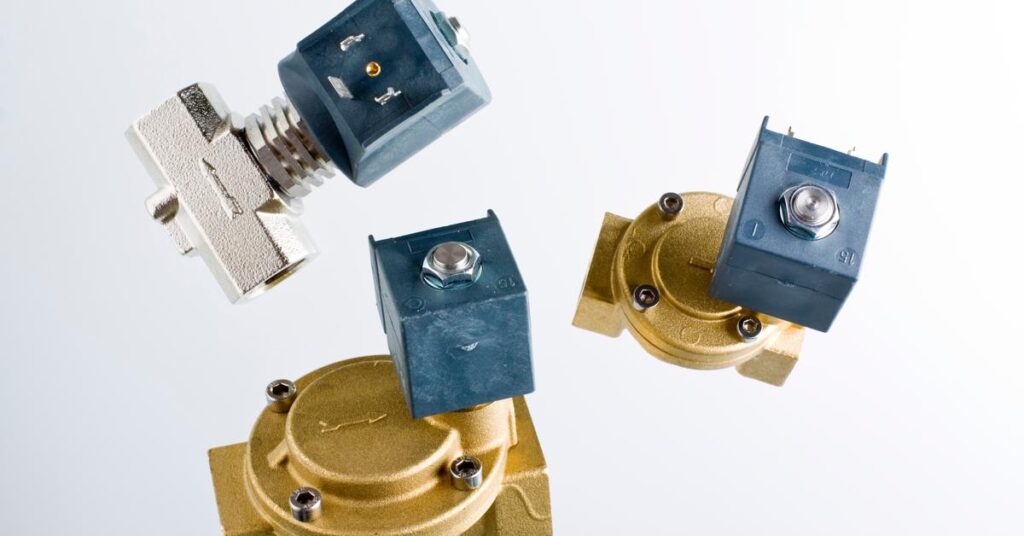
Coatings and Surface Treatments
Coatings support solenoid valves in corrosive environments. They act as barriers, shielding valve surfaces from agents that can cause chemical and physical degradation. Without protection, metals lose their integrity during acid, salt, or moisture exposure.
Epoxy coatings resist abrasion and chemical attacks, ideal for low to moderately aggressive media. Powder coatings form a hard, resilient shell that protects against moisture and minor mechanical impact. Teflon (PTFE) coatings provide exceptional chemical resistance, particularly in oil and gas sectors dealing with aggressive substances like sulfuric acid.
While coatings boost durability, they are not invincible. Regular inspections guarantee longevity because scratches or chips expose the underlying material to corrosive agents. Engineers must focus on careful upkeep to maximize the benefits of coatings.
Seal and Gasket Material Compatibility
Seals and gaskets prevent leaks and maintain flow control. Chemical compatibility between these parts and the medium they encounter determines whether the valve operates reliably or fails prematurely. Using incompatible materials can lead to swollen, cracked, or degraded seals that cause leaks or unsafe operations.
Ethylene propylene diene monomer (EPDM) works well with water and steam but deteriorates quickly after oil or solvent exposure. Viton, a high-performance fluorocarbon rubber, resists acids and alkalis but fares poorly in applications involving ketones or amines.
Nitrile (Buna-N) provides durability in hydrocarbon applications, such as oil or gas processing. These materials offer clear advantages but require careful selection based on the substances they will encounter.
Challenges in Corrosive Environments
High temperatures and pressures in corrosive environments amplify the challenges seals face. A valve working under extreme pressure and handling acidic fluids demands seals engineered to resist chemical attack and mechanical stress.
For example, highly specialized materials, such as Kalrez, may be necessary in facilities processing aggressive solvents. Keep in mind that they can withstand demanding conditions but require a higher investment.
The Importance of Valve Design in Corrosive Settings
Solenoid valve design affects how well it resists corrosion. Smart design features, such as smooth, non-porous surfaces and minimized crevices, prevent corrosive substances from accumulating.
For instance, a polished surface discourages the formation of pitting corrosion, which occurs in poorly finished areas. A valve for chemical handling should incorporate these features to remain functional in harsh conditions over time.
Designs that reduce contact points between dissimilar metals prevent galvanic corrosion, which occurs when two metals react electrochemically in the presence of a corrosive medium. Some valves feature insulating barriers or coatings in sensitive areas to minimize this risk. Engineers can avoid compatibility failures by selecting valves with few metallic interfaces in environments where risks of galvanic reactions remain high, such as marine applications or pipelines handling saline fluids.
Installation Best Practices To Minimize Corrosion
Proper installation practices enhance valve performance and prolong their life in corrosive environments. Positioning valves away from direct exposure to corrosive agents, and employing corrosion-resistant fittings mitigates damage.
Grounding systems prevent galvanic corrosion between dissimilar metals, especially in piping systems that feature aluminum and stainless steel. Moreover, regular monitoring of mounting hardware for signs of wear guarantees consistent protection. For example, using Teflon-lined piping and correctly orienting the valve reduces exposure and improves service life in a facility handling caustic substances. Overall, implementing thoughtful installation practices safeguards against premature failures.
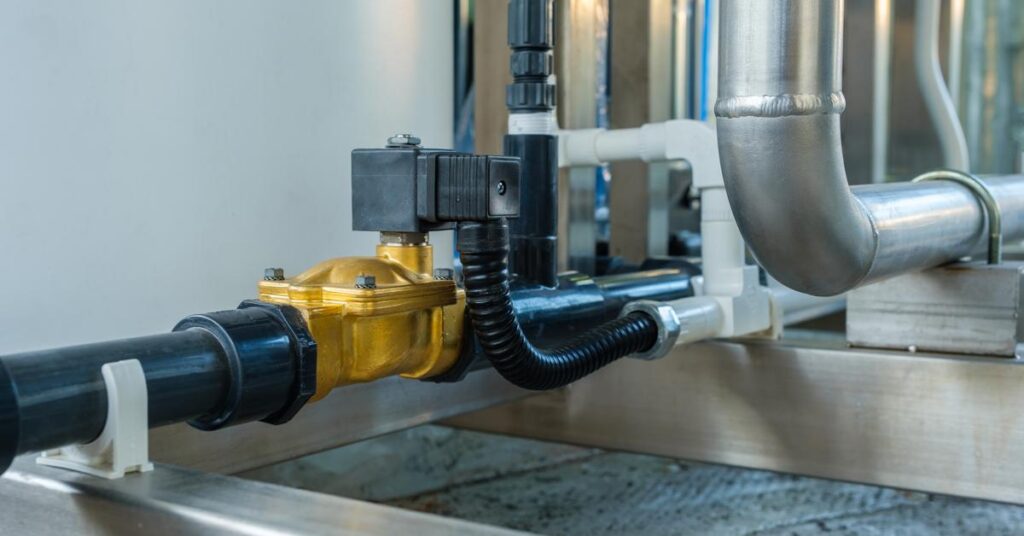
How To Choose the Right Valve for Your Needs
At Solenoid Systems, we specialize in manufacturing solenoids that suit your applications, including those in corrosive environments. Choosing the ideal valve begins with analyzing the media’s chemical properties, operating temperatures, and pressures. Our team uses this information to design customized solutions that meet your exact needs.
We offer guidance on selecting corrosion-resistant materials and advanced coatings. From handling aggressive fluids to ensuring long-term reliability, every valve will perform optimally in its environment.