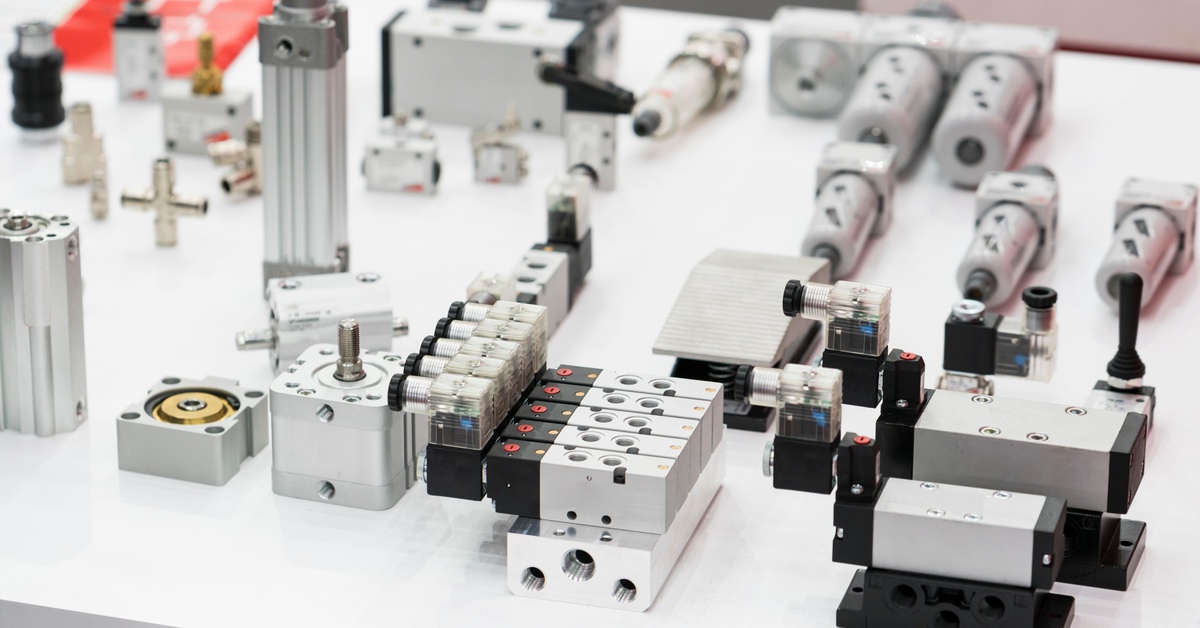
Automated systems depend on valve performance to regulate flow, execute commands, and respond to real-time process demands. Pneumatic and solenoid valves offer different strengths depending on the environment, application, and long-term system goals.
Engineers comparing technologies need more than feature lists—they need a clear view of where each option delivers value and where it introduces limitations. Choosing correctly requires aligning valve function with energy use, maintenance expectations, response time, and total lifecycle cost.
Response Time and Activation Speed
Solenoid valves offer extremely fast actuation by responding to electrical signals with nearly instantaneous internal movement. Their speed benefits automated dispensing, medical equipment, and timed-release systems that require precise flow interruption. The speed of valve cycles and synchronized system behavior across complex platforms highlight some of the pros and cons of pneumatic versus solenoid valves in high-speed environments.
Pneumatic valves provide smoother transitions in motion control applications where gradual actuation reduces mechanical wear. Air pressure-based systems excel in industrial environments where rapid shifts are less important than consistent physical force. Some high-end pneumatic setups also allow fine control of acceleration or deceleration, which aids applications involving sensitive mechanical loads.
Electric solenoids, when used in high-cycle systems, can generate heat that affects surrounding components and coil longevity. Without thermal management, compact systems may experience premature failure or drift due to internal heating during extended duty cycles. Environments with high ambient temperatures increase the need for cooling systems or spacing to maintain performance.
Pneumatic valves suffer from air delay, especially when operating across long airline paths or when air sources fluctuate under peak demand. In fast-paced industrial lines, those delays can cause timing issues that lead to rejected parts or inefficient sequencing. Compressors may compensate, but the complexity adds system cost and diagnostic burden.
Energy Consumption and System Efficiency
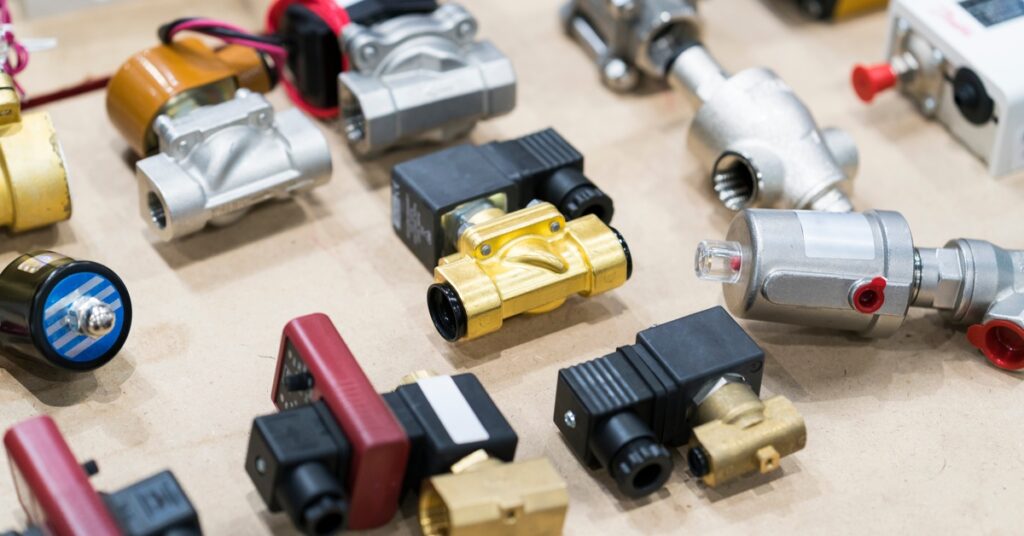
Solenoid valves typically consume power only during the actuation window, especially when using latching configurations. In applications where power control matters, such as portable units or energy-conscious manufacturing, solenoids reduce operating costs without sacrificing speed. Advanced controllers monitor current draw and optimize timing, making them highly efficient in tight energy envelopes.
Pneumatic systems deliver reliable power without electricity at the valve site, which benefits hazardous environments or installations where running electrical lines adds complexity. Compressed air drives multiple actuators simultaneously with centralized control, which reduces wiring and simplifies circuit design. In some high-load systems, air control remains more practical due to consistent mechanical delivery.
Solenoid setups with high duty cycles still require power conversion, which can introduce inefficiencies and losses depending on the power supply used. Long-duration actuation also increases energy draw unless managed by pulsed signals or controller feedback loops. Larger coils add thermal and current challenges that require attention during design.
Pneumatic networks waste energy through leakage, regulator drift, or continuous compressor cycling when system demand remains low. Undetected leaks can cost thousands annually, particularly in facilities running air systems around the clock. Performance issues often go unnoticed until they impact throughput or safety because air pressure drops slowly.
Maintenance and System Complexity
Pneumatic systems introduce multiple maintenance points. Lines, regulators, dryers, fittings, and the compressor itself all require scheduled checks. Problems such as condensation or oil buildup reduce system lifespan, and diagnosis often involves time-consuming inspection across multiple nodes. Skilled technicians must isolate drops in pressure or erratic actuator behavior using test gauges and flow monitors.
Solenoid valves offer a compact footprint with fewer external dependencies, which reduces points of failure and simplifies servicing. Coil replacement, seal swaps, and cleaning procedures often happen without disconnecting the entire valve body. Integrated status indicators diagnose electrical issues quickly for reduced downtime during fault isolation.
Pneumatics operate well in dirty or explosive environments where electrical systems may spark or fail. Since air control relies on physical force rather than voltage, pneumatic valves resist failure under dust, vibration, or chemical exposure. For many outdoor or industrial applications, that durability justifies the additional complexity of air support equipment.
Each setup requires a different maintenance mindset. Understanding the pros and cons of pneumatic versus solenoid valves helps teams select the right platform for their environment and staffing. Choosing incorrectly often means overbuilding infrastructure or underestimating labor costs. Preventive maintenance schedules must account for either electrical testing or airline integrity depending on the platform chosen.
Application Flexibility and Environmental Limitations
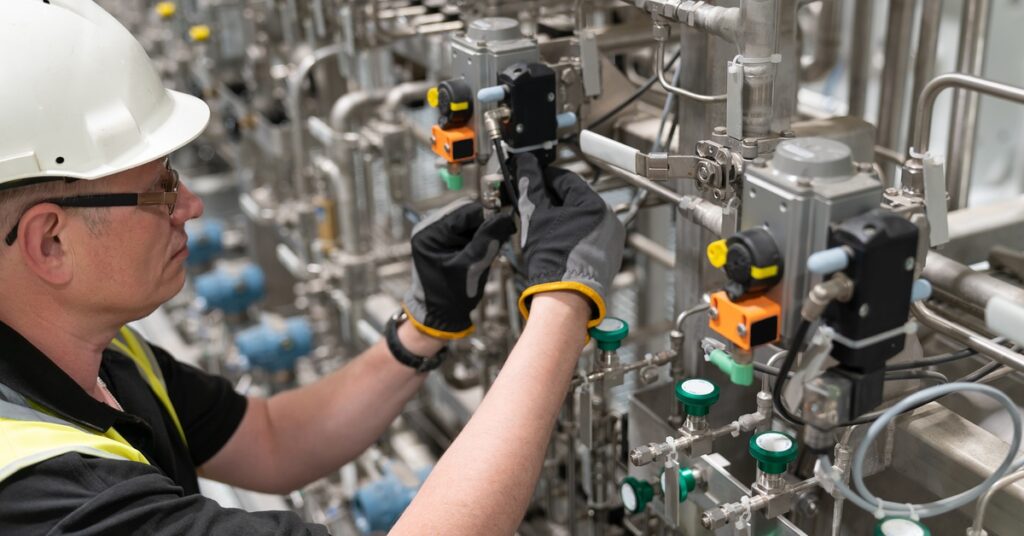
Solenoid valves integrate easily with control systems, PLCs, and electronic feedback loops that support modern smart manufacturing goals. They scale well in compact equipment, diagnostic tools, or digital systems where precise flow timing or low-voltage operation is essential. Many solenoids ship with modular coils or sensor-ready bodies for tight controller integration.
Pneumatic valves tolerate extreme environments with dust, temperature, vibration, or chemical exposure without suffering electronic interference or voltage failure. Mining, painting, or marine applications benefit from pneumatic valve resilience and insensitivity to electrical variation. When reliability under physical stress matters more than signal compatibility, air-based systems may perform better.
Solenoids may struggle in high-moisture, vibration-heavy, or flammable environments. But they can typically handle various environments when upgraded with specialty seals, coatings, and enclosures. System designers must account for ingress protection ratings, cable shielding, and heat transfer in high-density electrical environments. In industries like oil and gas, solenoids often require more customization to meet safety codes.
At Solenoid Systems, we offer custom solenoids for manufacturers across the automotive, aerospace, medical, and industrial sectors. Our team works directly with clients to develop valve solutions that match real-world operating demands, safety requirements, and system integration needs. Whether you require pulse actuation or precision timing, we support it with tested, scalable components.
Cost Factors and Installation Requirements
Pneumatic systems demand up-front infrastructure investment. Compressors, tanks, dryers, and regulator panels increase total install time and cost. For larger operations, those systems make sense when air tools or multiple actuators run concurrently. Startup costs balance out when the network supports long-term mechanical output and durable gear.
Solenoid systems install quickly and integrate directly into modern electronics without separate air lines or bulky infrastructure. Small-format valves bolt into position and wire into existing control systems, reducing installation hours significantly. In cleanroom or diagnostic environments, that speed translates to reduced disruption and faster commissioning.
Pneumatics carry ongoing costs from compressor wear, air leakage, and downtime during line maintenance or upgrades. If redundancy isn’t designed into the system, a compressor failure halts multiple processes simultaneously. Facilities need trained technicians to inspect regulators, service compressors, and calibrate line pressure regularly.
Solenoid valves incur fewer indirect costs, but higher-quality models may require voltage converters or environmental sealing to withstand demanding use. Coil selection and wiring paths must match controller capabilities, or reliability suffers. If overlooked, electrical compatibility issues introduce noise, heat, or short cycling that limits long-term performance.
Every automated system has different goals, and no valve offers a universal solution. Engineers evaluating valve options must match actuation speed, maintenance demands, and environmental tolerance to the application’s requirements.
At Solenoid Systems, we help industrial teams choose and customize valve solutions that align with performance, durability, and cost expectations—backed by decades of design and application expertise.