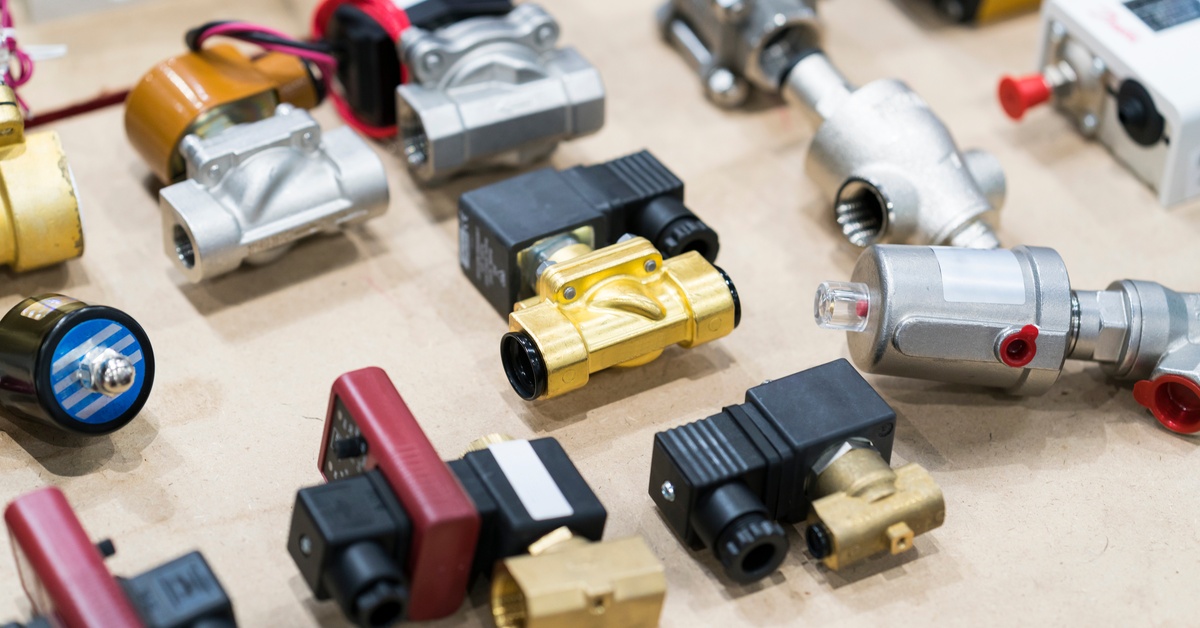
Seals are vital components in solenoid valve systems that enhance performance and reliability. They help with managing the flow of fluids in medical devices and supporting mechanical stability in industrial machinery; we cannot overstate the importance of their role! By examining how they control leaks, enhance precision, and boost durability, you’ll learn why seals are indispensable for optimizing solenoid valve functionality.
Prevents System Leaks
Leaks can undermine system efficiency, compromise safety, and lead to contamination in sensitive applications. Seals eliminate these risks by creating an airtight barrier that stops fluids or gases from escaping the system. Professionals in pharmaceuticals and food production depend on superior sealing to protect product integrity and meet safety standards.
High-quality materials play a role in leak prevention. Ethylene propylene diene monomer (EPDM) and nitrile resist wear, pressure, and chemical degradation and offer reliable performance under different conditions. By prioritizing these materials, you enhance system longevity and minimize disruptions caused by maintenance or downtime.
Designing efficient systems that prevent leaks highlights the importance of seals in solenoid valve functionality. Substandard seals often lead to frequent malfunctions, such as overheating, driving up operational costs.
The integration of advanced sealing technology, such as high-performance elastomers and thermoplastics, stabilizes system pressure and prevents contamination. Improved material strength and resistance to wear help business leaders avoid unexpected equipment failures that disrupt productivity.
Provides Accurate Flow Control
Seals affect flow control accuracy in solenoid valves, particularly in precision-driven industries. Applications in medical equipment, irrigation setups, and energy grids require consistent flow regulation with high-quality sealing components. Poor-quality seals create gaps and result in erratic operations or system failures. The choice of seal material affects flow control tolerances.
Fluoroelastomers (FKM) are resistant to aggressive chemicals. Silicone is flexible and functions well under pressure fluctuations. Engineers rely on these properties to support complex systems.
Acknowledging the importance of seals in solenoid valve functionality helps professionals achieve better flow regulation and performance optimization. High-grade sealing reduces error rates, stabilizes outputs, and contributes to smoother interactions between systems.
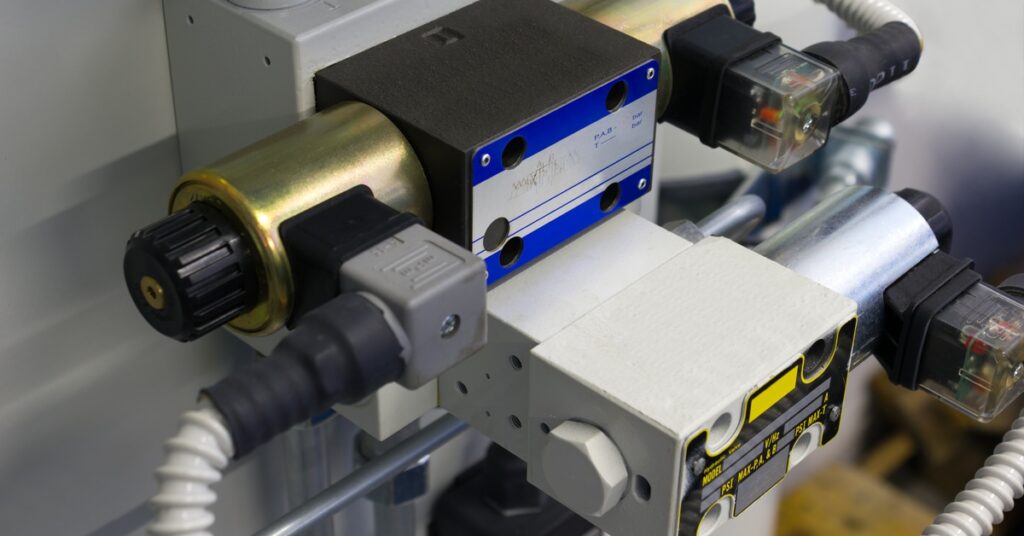
Enhances Durability of Solenoid Valves
Seals shield solenoid valve components from contamination, wear, and chemical damage, which would otherwise shorten operational lifespans. Protective barriers prevent abrasive particles and corrosive substances from compromising sensitive valve mechanisms. This improves long-term reliability and minimizes disruptions caused by premature component failures.
High-output manufacturing facilities use durable seals to reduce equipment maintenance and downtime. Systems using polytetrafluoroethylene (PTFE) or nitrile resist cracking, hardening, and degrading under repetitive use. This extends their performance without frequent interventions. Investing in such materials can transform operational efficiency for professionals in the automotive and industrial sectors.
Engineers rely on seals that withstand environmental challenges, including extreme temperatures and high pressure. For instance, professionals in the oil and gas industry do tough work, and equipment benefits from seals with thermal and mechanical stability. Solenoid Systems is an expert water solenoid valve manufacturer that develops durable sealing solutions tailored for different operational needs and long-lasting valve efficiency.
Provides Reliability in Extreme Conditions
Reliable seals allow solenoid valves to perform consistently under extreme operating conditions. Aerospace applications and high-pressure pipelines place immense stress on components, so they require seals that withstand drastic temperatures or pressures.
Material selection plays a crucial role in reliability during extreme operations. PTFE combines chemical resistance with structural stability to maintain functionality where traditional materials fail. Similarly, EPDM maintains flexibility under various thermal conditions, providing assurance against sudden failures.
Adopting advanced sealing solutions prevents catastrophic malfunctions that risk damaging the entire system. Equipment for deep-sea missions, for instance, benefits from seals that deliver dependable performance under pressure.
Reduces Costs and Minimizes Downtime
Maintenance issues and repairs can incur high expenses and take time. Seals reduce these inefficiencies by extending system reliability. Long-lasting seals require fewer replacements and streamline performance. Silicone or nitrile seals offer cost advantages because you won’t have to replace them frequently.
Preventive approaches to maintenance amplify the benefits of durable seals. By monitoring wear and tear and replacing components in a timely manner, you can prevent equipment breakdowns.
Balancing engineering quality with costs is a smart strategy. Custom seals that support workflow adaptability allow you to minimize disruptions while staying productive.
Adapts to Dynamic Conditions
Dynamic operational conditions create challenges for solenoid valves. Fluctuations in temperature, pressure, or flow rate demand seals that remain stable while responding to adjustments. Purpose-built seals reinforce resilience against dynamic stressors.
Material flexibility makes reinforced rubber indispensable for these environments. Industrial HVAC systems, for example, have seals that stay intact amid thermal and pressure shifts. Modular design strategies further expand adaptability to industry-specific applications.
Engineers and manufacturers value adaptable seals for their ability to integrate seamlessly into different environments. Reliable solutions optimize complex setups, secure system stability, and improve workflow efficiency.
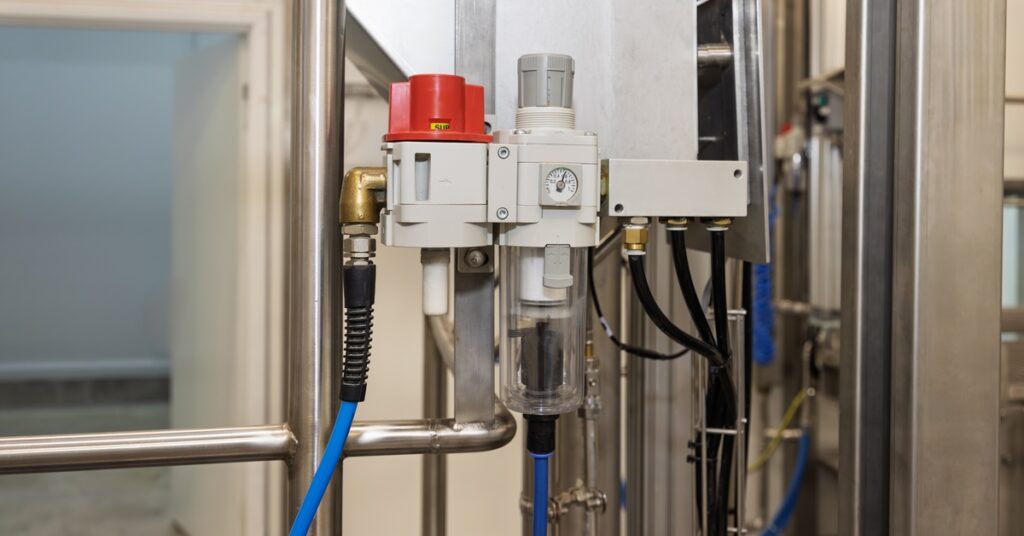
Supports Efficient and Sustainable Operations
Efficient sealing design enhances sustainability by reducing waste and extending component durability. Businesses with green practices may adopt eco-friendly seals in order to reduce the environmental impact of operations. Innovation prioritizes materials that improve both performance and ecological responsibility.
Renewable energy systems benefit from new seals, too. Solar and wind energy components lose functionality due to leaks or friction, but quality seals mitigate energy losses. High-quality materials support a company’s commitment to sustainable improvements without compromising productivity.
Sustainable approaches to sealing may lead to pollution reduction and workflow optimization. Recyclable or low-carbon materials reduce emissions and comply with environmental policies. Your industrial priorities will remain aligned with your ethical goals without trade-offs on reliability.
Professionals in the automotive and aerospace industry use biodegradable or recyclable seals made of PTFE composites to achieve long-term environmental goals. Advanced rotary seals in wind turbines reduce lubricant leakage, maintenance frequency, and environmental contamination.
Low-friction, durable sealing materials reduce mechanical resistance and heat buildup in engines or pumps. Less friction helps professionals lower emissions and maintain full operational capacity by decreasing energy consumption and fuel use.
Prioritize Your Valve Seals Today
Seals optimize solenoid valve systems by preventing leaks, controlling flow, and enhancing durability. Their contributions extend to the most demanding environments, where maintaining reliability under dynamic or extreme conditions sets the benchmark for performance. Professionals seeking quality and efficiency recognize the value of durable and optimized sealing solutions.
Working with professional valve manufacturers at Solenoid Systems offers expert sealing solutions that meet your operational needs. As you can see, custom-engineered seals perform consistently across many industries. Rely on solutions from Solenoid Systems today for long-lasting and efficient valve performance.