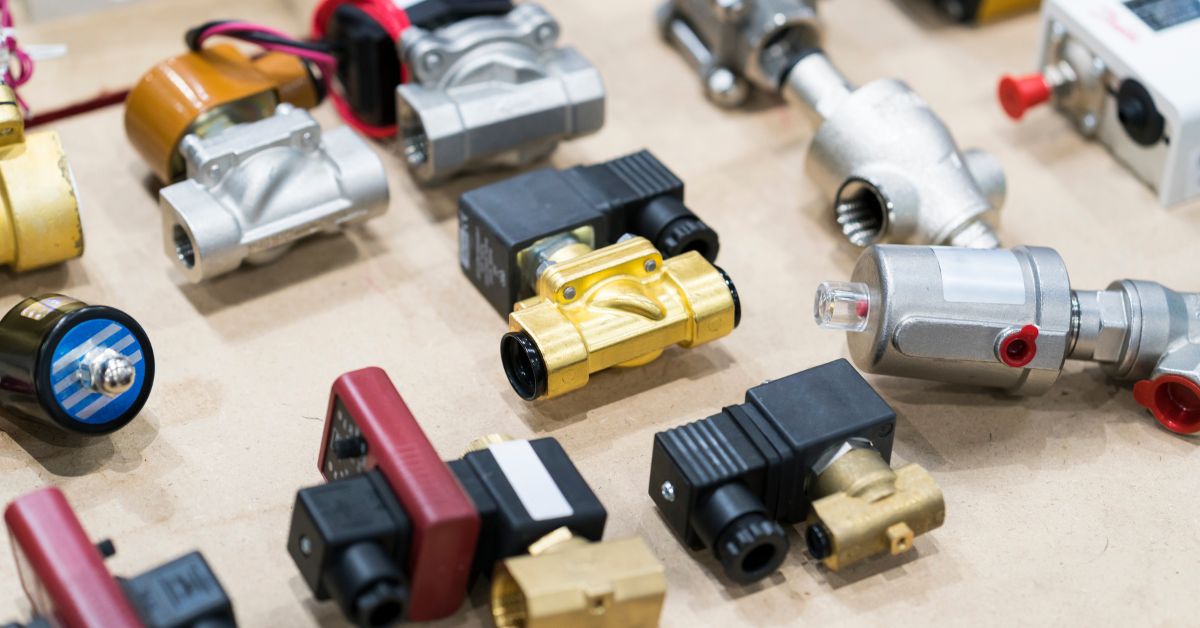
Solenoid valves support fluid control systems, regulating the flow of liquids and gases. These valves consist of an electromagnetic coil and a movable plunger, which opens or closes a valve seat to control fluid flow. Industries rely on solenoid valves for reliability, but selecting the right material can impact performance. Let’s assess stainless steel, brass, and plastic solenoid valves to understand their benefits, drawbacks, and application suitability.
Stainless Steel Solenoid Valves
Stainless steel solenoid valves have remarkable durability and performance. Designed for high-demand environments, they offer exceptional resistance to wear and tear, making them ideal for industries that require constant fluid flow under challenging conditions.
Their robust construction ensures longevity, reducing the need for frequent replacements or repairs. Industries that deal with harsh chemicals or abrasive substances generally choose stainless steel for its ability to withstand such rigors without compromising functionality.
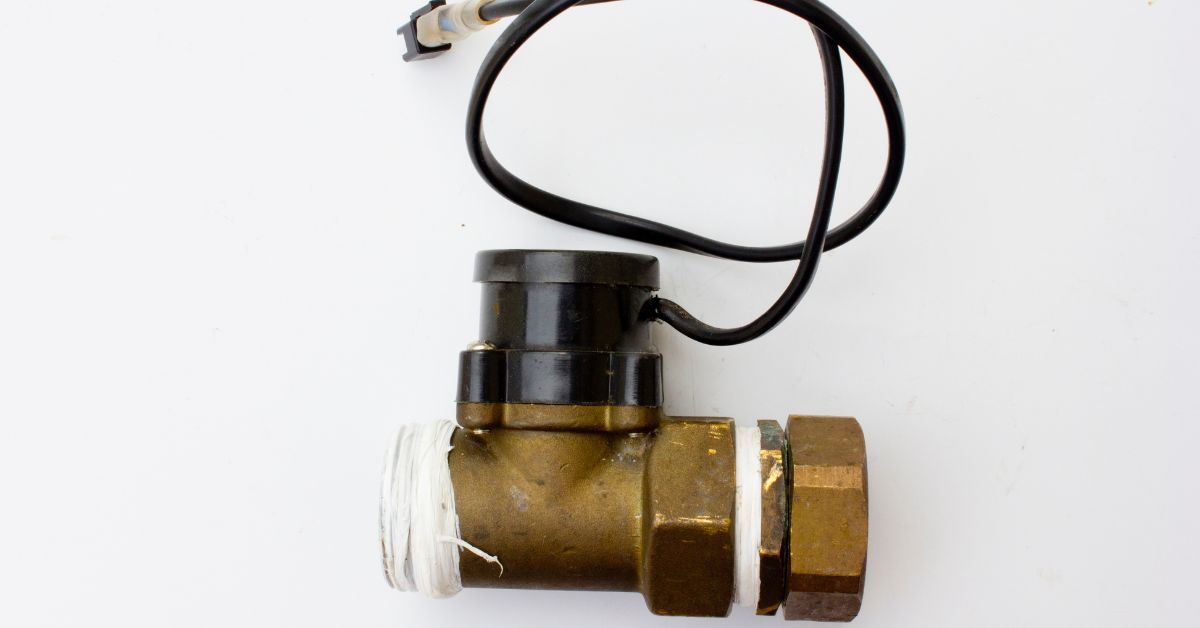
Corrosion Resistance and Applications
The corrosion resistance of stainless steel makes these valves indispensable in environments where exposure to corrosive agents occurs regularly. Chemical processing plants rely on them to maintain integrity in their pipelines.
Pharmaceutical manufacturing also benefits from stainless steel solenoid valves because they can handle clean, sterile conditions without the risk of contamination. Additionally, these valves withstand high temperatures and pressures effortlessly, making them a staple in processes that demand rigorous standards.
Cost and Considerations
While stainless steel solenoid valves excel in performance, their cost reflects their premium nature. This material comes with a higher price tag than other options, which can influence budgeting decisions.
However, industries prioritizing reliability and long-term value consider this investment worthwhile. Food and beverage sectors, for instance, recognize stainless steel as a reliable choice that ensures product safety and compliance.
Brass Solenoid Valves
Brass solenoid valves offer versatility across various applications. Known for their balance of strength and malleability, these valves adapt well to different configurations and modifications.
This ease of machining makes them a preferred choice in industries that require custom solutions or frequent adjustments. HVAC systems, for example, utilize brass valves to facilitate climate control, thanks to their adaptability and resilience.
Corrosion Resistance and Limitations
Brass provides moderate resistance to corrosion, ideal for non-corrosive liquids and environments. Water management systems benefit from brass solenoid valves because they can handle urban water supplies without degradation. However, brass may fall short in handling highly acidic substances, which limits its application in certain chemical processes.
Cost Effectiveness and Applications
Cost effectiveness is a significant advantage of brass solenoid valves. Their affordability and sufficient durability make them a good choice for residential and commercial settings. In these contexts, the emphasis on budget-friendly solutions meets the need for reliable functionality.
Plastic Solenoid Valves
Plastic solenoid valves thrive in applications where weight and corrosion resistance take priority. Their lightweight nature facilitates easy installation, reducing labor costs and time. This characteristic supports sectors like agriculture, where irrigation systems require frequent updates and maintenance.
The corrosion resistance of plastic also makes it a preferred choice for water treatment facilities, where longevity and reliability matter.
Temperature and Pressure Limitations
While plastic valves offer many benefits, they come with specific limitations. They manage a narrower range of temperatures and pressures than their metal counterparts, impacting their suitability for certain industrial applications.
Industries requiring high-pressure systems or extreme temperature management may find plastic unsuitable. However, plastic valves meet requirements for non-critical applications without needing heavy-duty specifications.
Economical Solutions and Applications
Do not overlook the economic advantage of plastic solenoid valves. They provide a cost-effective solution for projects that prioritize budget constraints and ease of handling.
Noncritical fluid management systems, such as domestic water distribution or small-scale agricultural setups, benefit from the affordability and practicality of plastic valves. Their ease of use aligns with projects focused on efficient resource management without compromising on essential performance.
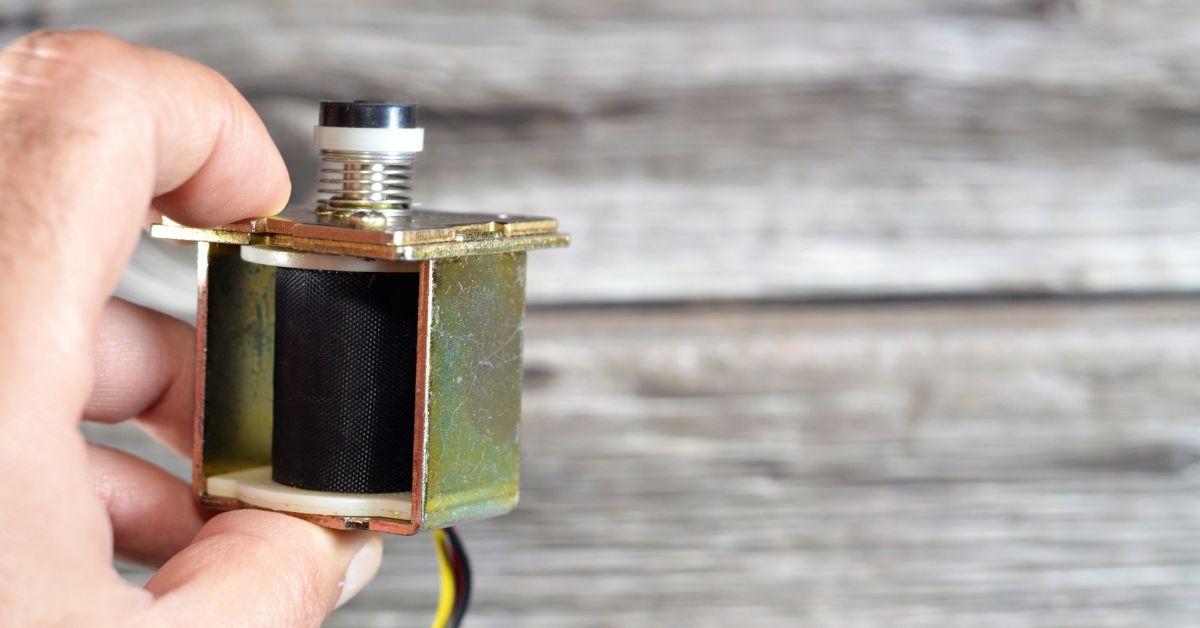
Common Industries and Applications
As mentioned, stainless steel, brass, and plastic solenoid valves excel in specific applications. Here’s an overview of industries and applications that benefit from the solenoids:
Chemical Processing
In chemical processing, stainless steel solenoid valves are indispensable. These valves excel under high pressure and corrosive conditions, providing reliable performance where lesser materials might falter.
The robustness of stainless steel ensures that operations continue smoothly without frequent interruptions for maintenance or replacements. Acid and solvent plants depend on these valves for their superior resistance to harsh substances.
HVAC Systems
Brass solenoid valves find extensive use in HVAC systems, offering a balance of cost-effectiveness and reliability. Their malleability allows for custom configurations and easy integration into complex climate control systems.
Brass withstands moderate temperature variations, making it ideal for controlling airflow and water circulation in heating and cooling systems. This makes brass suitable for use in residential and commercial properties.
Irrigation and Water Treatment
Plastic solenoid valves support irrigation and water treatment applications. Their lightweight construction and corrosion resistance are excellent for managing water distribution across agricultural fields and gardens.
The water solenoid valve plays a key role in automating irrigation systems, ensuring optimal water usage and conservation. In water treatment facilities, plastic’s resistance to corrosion prolongs valve life, contributing to long-term operational efficiency.
Food and Beverage Processing
Stainless steel solenoid valves dominate the food and beverage industry, where hygiene and safety standards require robust solutions. These valves control steam and other fluids in processing environments, maintaining precise conditions necessary for quality assurance.
The non-reactive nature of stainless steel prevents contamination, which is essential for processes involving consumable goods. Breweries, dairies, and processing plants rely on these valves to uphold product integrity.
Agricultural Applications
Plastic solenoid valves play an important role in agriculture, particularly in systems that require lightweight solutions. Farmers utilize these valves to control irrigation channels, adapting water flow to meet the demands of different crops.
Easy handling makes plastic a go-to option for managing small to medium-sized agricultural operations. These valves align with the industry’s resource efficiency goals, ensuring effective water management in the field.
Cost Analysis and Long-Term Value
When evaluating solenoid valves, understanding the cost implications of stainless steel, brass, and plastic provides insight into their long-term value. Stainless steel valves have a higher initial cost because of their superior corrosion resistance.
However, industries that demand reliability and low maintenance find the investment worthwhile over time, as these valves withstand harsh environments with minimal wear.
Brass valves offer a more budget-friendly solution, balancing costs with adequate performance for less demanding applications. They suit projects that prioritize upfront savings and moderate operational conditions.
Although the most economical choice initially, plastic valves may incur higher long-term costs in rigorous settings due to their limited lifespan and lower durability. Plastic offers a cost-effective solution for applications that prioritize lightweight construction and corrosion resistance without extreme demands.
Ultimately, assessing the balance between initial investment and long-term operational expenses helps determine the most cost-effective choice for specific needs.