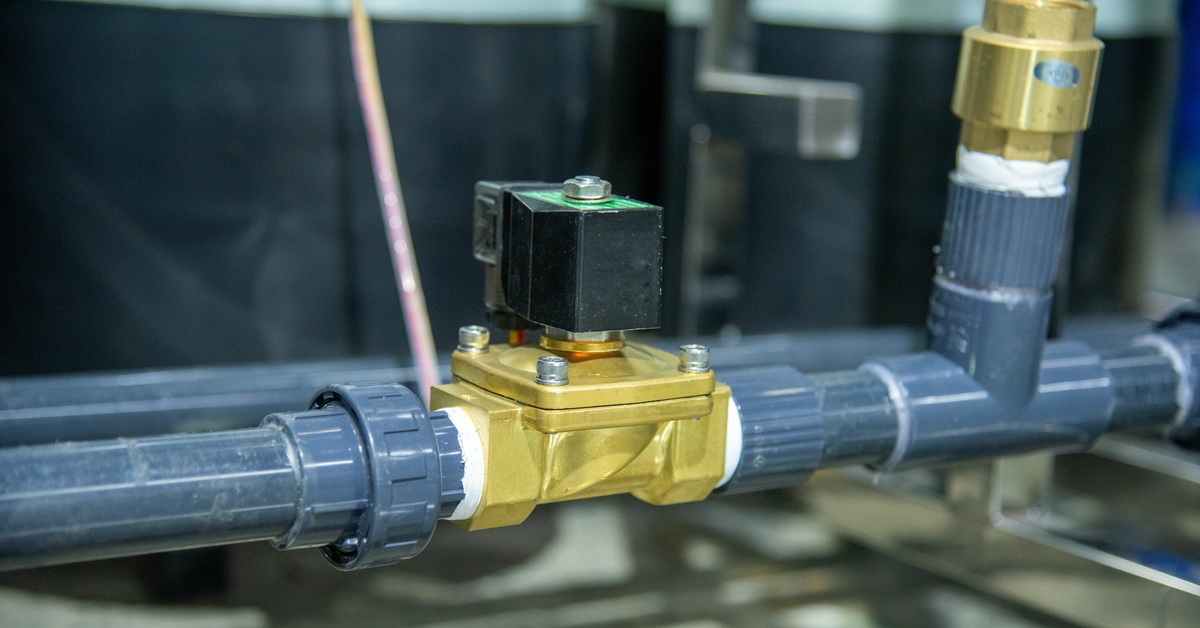
Solenoid valves support many mechanical and industrial systems, offering trusted performance and reliability. Peak-and-hold solenoid valves take this reliability a step further by providing a specialized, energy-efficient upgrade. By exploring these advanced models, you can unlock their benefits, including improved system performance and better energy management. For deeper insight, here’s a comprehensive guide on what you should know about peak-and-hold solenoid valves.
What Are Peak-and-Hold Solenoid Valves?
Peak-and-hold solenoid valves operate through two distinct power phases. The “peak” phase sends a high-power current to quickly activate the valve, enabling its fast response. Then, the system shifts to the “hold” phase, maintaining actuation with a lower power level. This separation between actuation and maintenance ensures efficient energy use.
Unlike traditional solenoid valves that rely on consistent power to maintain operation, these models reduce strain on electrical components while ensuring reliable function. For example, in a hydraulic system requiring fast responses, these valves minimize power draw without affecting system performance.
Key Technical Specifications
One of the standout features of peak-and-hold solenoid valves is their rapid response. The “peak” phase delivers high power to activate the valve quickly, which is essential for applications requiring immediate actuation.
For instance, industrial automation systems that rely on precise timing for tasks like packaging or material handling benefit from measurable improvements in speed. These valves reduce delays, allowing production lines to operate smoothly and efficiently without risking errors or interruptions.
Voltage and Current Requirements
Another thing to know about peak-and-hold solenoid valves is that they operate with distinct voltage and current ranges for their two power phases. Systems using these valves typically rely on controllers to manage power modulation.
The peak phase uses an initial surge of current to engage the valve, followed by a reduced level during the hold phase. This setup ensures optimal performance without overloading electrical circuits.
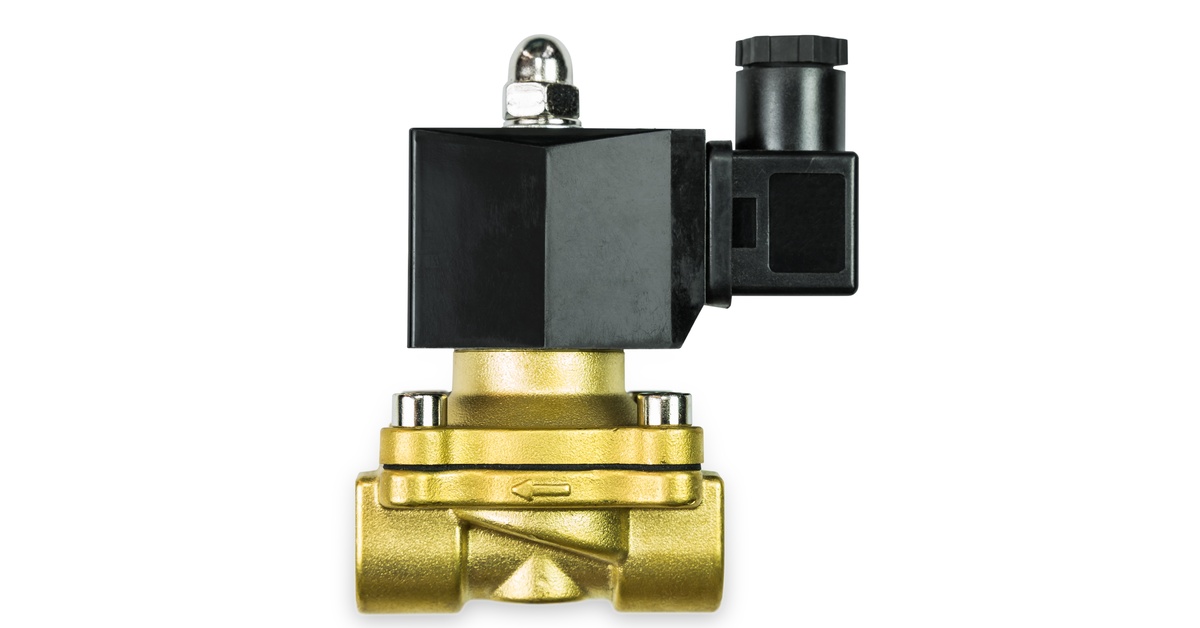
Cycle Lifespan
The solenoid valves have longer lifespans than traditional models due to reduced stress during operation. Manufacturers conduct rigorous tests to confirm their durability through several actuation cycles. Systems in various industries depend on their extended reliability to reduce the frequency of replacements and minimize downtime. Their unmatched service life ensures they perform under consistent, high-frequency demands.
Noise Reduction
Compared to traditional solenoid valves, peak-and-hold models reduce noise during operation. Their power modulation process creates smoother transitions between power phases, which minimizes vibrations and operational sounds, such as clicking. Noise-sensitive environments like medical facilities or production floors that require quiet operations benefit substantially.
Advantages of Peak-and-Hold Solenoid Valves
Peak-and-hold solenoid valves excel through their ability to manage energy intelligently. They activate with a high-power surge during the peak phase and then shift to a low-power hold phase to maintain operation.
This transition conserves energy without compromising functionality. For instance, in industrial automation systems running non-stop, the hold phase reduces electricity usage. Over time, this efficiency lowers operating costs, which is critical for businesses seeking to optimize long-term savings.
Minimized Heat Generation
Traditional solenoid valves generate excess heat due to constant high power, creating unnecessary strain on components. Peak-and-hold models, however, reduce this heat during the hold phase.
A cooler operation protects internal parts, such as seals or coils, from wear and tear. For example, hydraulic press valves will last longer because they operate under controlled heat conditions, boosting overall system reliability.
Improved Longevity
Because these valves operate with reduced power during the hold phase, they minimize mechanical strain on the components. This optimized usage reduces wear over time.
Automotive systems and medical equipment demand durability for long-term operation, and these models deliver exactly that. Reduced strain directly translates to fewer replacements and lower maintenance costs.
Compact Yet High-Performance Design
Peak-and-hold solenoid valves combine precision and efficiency in compact packages. Their small size allows them to fit into systems where traditional solenoid valves might prove impractical.
Pneumatic solenoid valve manufacturers typically recommend these smaller designs for applications with limited space but high-performance needs. For example, robotic systems benefiting from these valves maintain accuracy while adhering to tight spatial constraints.
Applications of Peak and Hold Solenoid Valves
The automotive industry incorporates these valves in systems such as fuel injection and transmissions. Peak-and-hold solenoid valves ensure precise fuel delivery, optimizing engine performance while minimizing excess usage.
Vehicles equipped with these systems operate more efficiently and produce cleaner emissions. Additionally, their role in transmission systems enables smoother gear shifts in consumer and commercial vehicles.
Moreover, medical devices require accuracy, reliability, and energy efficiency, all of which align with the capabilities of peak-and-hold solenoid valves. For instance, infusion pumps depend on controlled actuation to deliver precise fluid volumes to patients.
Portable medical equipment, like oxygen concentrators, benefits from these valves’ low energy consumption, extending battery life.
Industrial Automation and Aerospace
The solenoid valves cater to the demands of industrial automation, where response times and energy efficiency determine success. Packaging machines and pneumatic conveyor systems rely on the rapid actuation these valves provide. Their ability to maintain steady functionality with low heat generation ensures consistent operations, even in high-cycle environments.
Aircraft operate under conditions demanding reliability and weight-efficient solutions. Peak-and-hold solenoid valves, with their compact and lightweight construction, fit seamlessly into fuel management and hydraulic systems. Their lower energy consumption also supports the aircraft’s broader goal of conserving fuel.
Maintenance Tips and Best Practices
Consistent inspections ensure peak-and-hold solenoid valves maintain optimal functionality over time. Examine seals, connectors, or electrical wiring for signs of wear or damage. A worn seal can cause fluid leaks, reducing system efficiency and safety. Addressing such issues during routine checks helps avoid disruptive failures and ensures uninterrupted operation.
Electrical input verification is essential for the peak-and-hold phases. The peak phase demands a high current for activation, while the hold phase requires reduced power for maintaining functionality.
Irregularities in these input levels may lead to delayed actuation or overheating. Verify and troubleshoot electrical connections regularly to ensure your system functions correctly. Well-calibrated controllers contribute to stable operations and prevent performance issues.
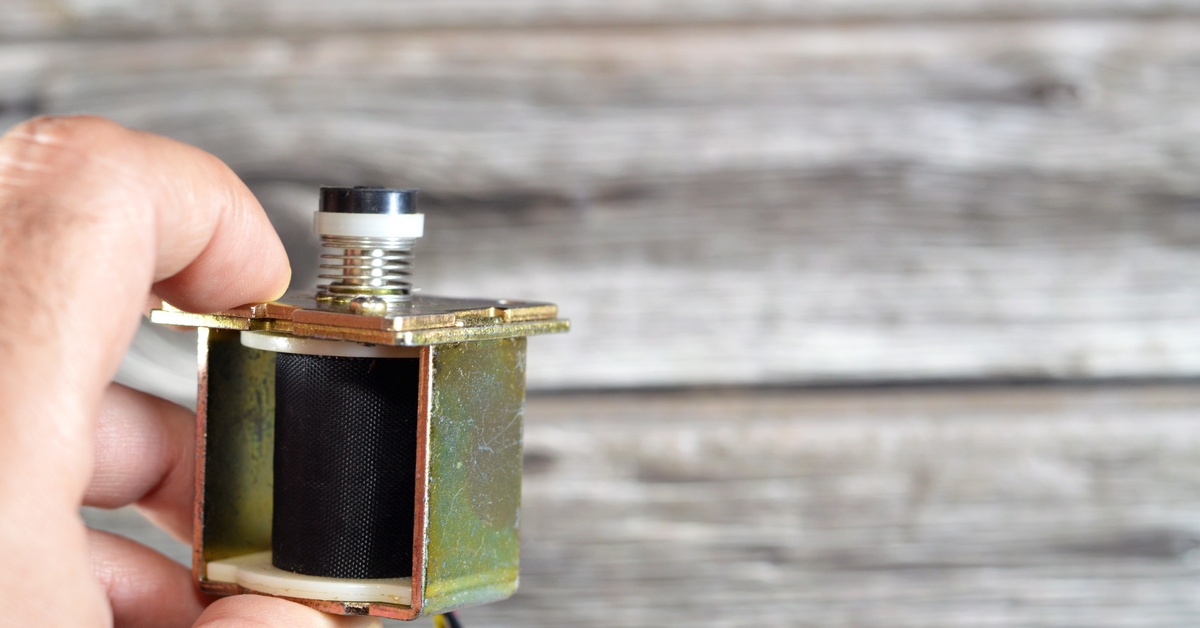
Cleaning Operational Areas
External debris and contaminants obstruct the functionality of peak-and-hold solenoid valves. Regularly clean the operational areas around these components to prevent blockages or damage. Applications in industries like oil and gas, where particulate buildup occurs frequently, benefit from thorough cleaning schedules.
System Testing
Testing peak-and-hold solenoid valves as part of the larger system ensures their integration with controllers and other components remains faultless. Assess actuation speeds, timing, and pressure levels to confirm precise operation. Regular system testing supports reliability while helping to catch potential issues before they escalate.
Final Thoughts
Peak-and-hold solenoid valves stand out for their ability to optimize efficiency and precision across diverse industries. Their innovative design supports high-performance systems, making them a smart choice for modern applications. By incorporating these valves, you can drive reliability and resourcefulness in your operations.