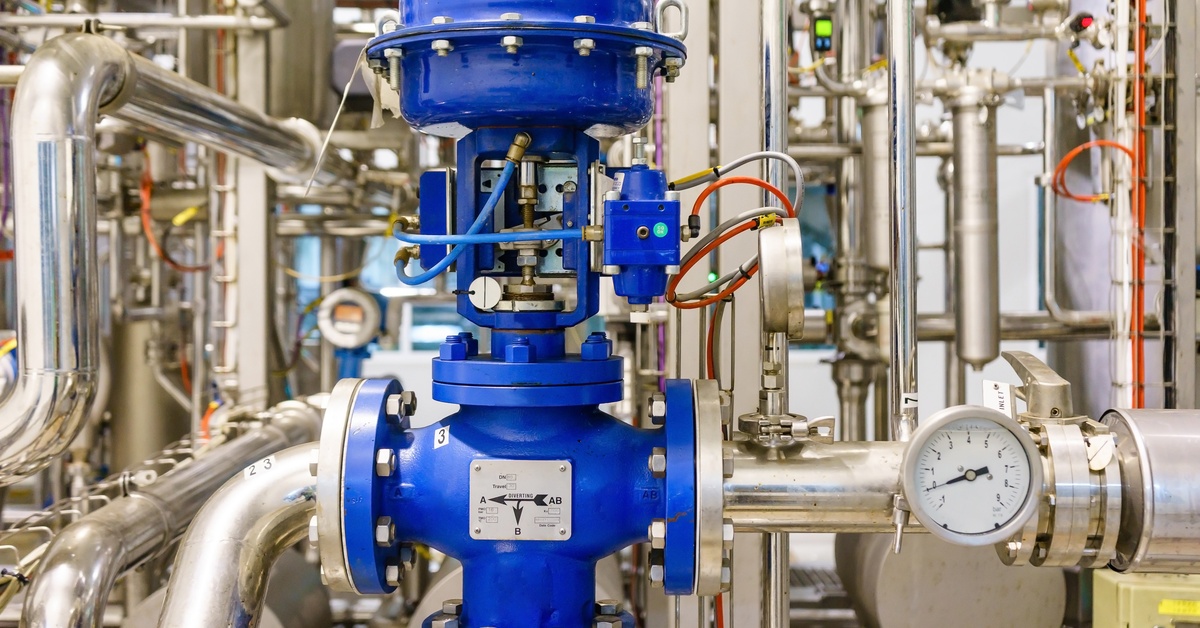
Extreme cold challenges even the most advanced valve systems across industries ranging from defense to medical equipment manufacturing. Latching valves become highly susceptible to freezing without the right combination of materials, geometry, and protective measures.
As temperatures fall, moisture condensation, stagnant fluid, and heat transfer loss combine to create ice formations that compromise valve actuation. Many system failures can be traced to overlooked thermal weak points. Every engineering team working in harsh environments must prepare proactively to eliminate those risks before they compromise long-term performance.
Identify Vulnerable Points in the System
System assessments must begin with a full thermal mapping of every fluid contact surface, housing, and joint. Connection points, especially where fluid enters or exhausts, typically introduce temperature drop zones where ice accumulation begins. Narrow passages or chambers exposed to ambient airflow without shielding create isolated cold spots that lead to internal valve malfunction.
Historical failure logs often reveal repeat patterns—locations in the system that freeze first or experience actuation lag during cold starts. Teams should mark those areas as critical and incorporate real-time thermal feedback sensors to track performance changes. One reliable way to prevent the freezing of latching valves in extreme cold involves auditing all mechanical connections and identifying every point where cold air or moisture could concentrate.
Thermal analysis should not rely solely on design software. Technicians should physically inspect equipment and collect performance data during varied load conditions. Comparing temperature trends across multiple installs gives insight to modify designs or reinforce protection on vulnerable nodes.
Poor placement also plays a role in vulnerability. Latching valves installed near ventilation outlets, open-air panels, or undersized enclosures suffer from greater exposure and wider temperature swings. Teams can relocate hardware or install shielding to protect critical units during downtime or low-circulation cycles. Structural repositioning of the valve often delivers better results than simply adding external heating.
Optimize Thermal Insulation at the Valve Level
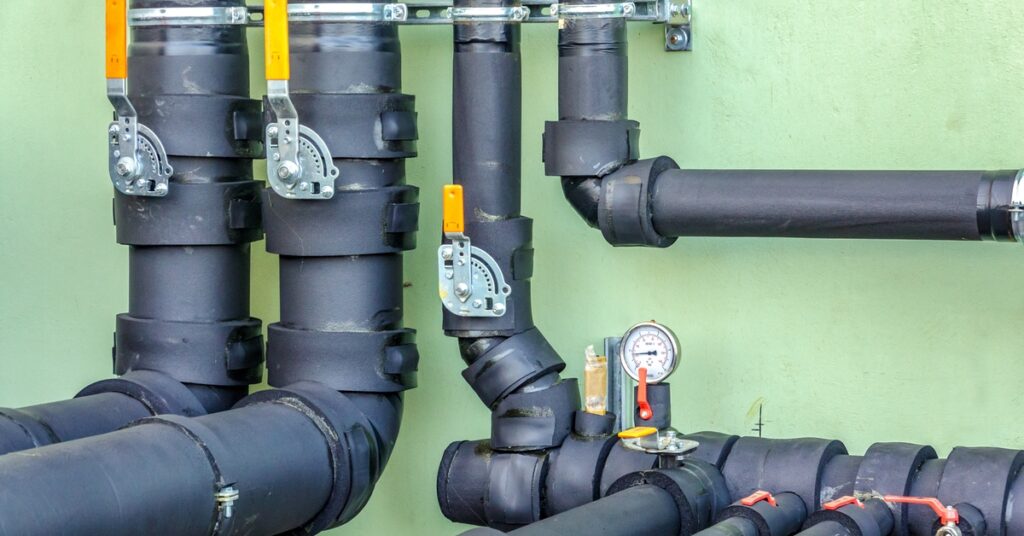
Standard foam wraps or basic insulation sleeves often fail under subzero conditions, particularly when systems cycle between hot and cold phases. Teams should select insulation based on the thermal inertia of the valve body, not simply the surrounding temperature range. For rapid-cycling applications, molded insulation with embedded vapor barriers provides tighter surface contact and better energy retention.
Industrial-grade aerogel wraps or silicone foam shields offer high R-values without interfering with access panels or mounting hardware. Custom-fitted jackets reduce air gaps and minimize heat escape at seams. Many manufacturers now specify insulation thickness as part of the valve housing spec to eliminate mismatch between components and thermal control systems.
Insulation can’t operate effectively without proper sealing. Small leaks in vapor wrap or poorly attached foam invite moisture intrusion and frost formation. Use pressure and moisture differential analysis to test sealing integrity after installation. While many strategies support performance, one proven way to prevent the freezing of latching valves in extreme cold is by applying well-fitted, closed-cell insulation that matches the operating environment.
Technicians must account for servicing needs during insulation selection. Removable jackets with durable closures support maintenance cycles without degrading over time. Pre-cut gaskets and modular panel access points allow operators to inspect or replace internal elements without dismantling the entire assembly. Equipment longevity improves when insulation works seamlessly with system ergonomics.
Redesign Valve Geometry To Reduce Ice Formation
Geometry directly impacts how fast a latching valve accumulates moisture or sheds thermal energy. Rounded edges, shallow chamber profiles, and fewer isolated cavities reduce ice formation risk. Minimize turbulence zones to prevent film condensation or pressure-driven fluid stagnation.
Flow channel width and curve profiles determine whether trapped air cools too quickly or leads to frost buildup. Baffles and guide vanes positioned too close to chamber walls often accelerate freezing. Removing turbulence or stagnant vapor pockets delivers faster response and better freeze resistance.
Compact housings transfer heat evenly and retain warmth more effectively than oversized builds with distant chamber zones. Optimized size also simplifies insulation and heating system integration.
At Solenoid Systems, we offer advanced proportional solenoid valve design for clients who demand high performance in extreme environments. We custom-engineer valve architecture to reduce thermal loss while improving control precision. Our engineering team works directly with OEM partners to develop systems that maintain reliability in the coldest field conditions.
Incorporate Active Heating Methods Where Needed
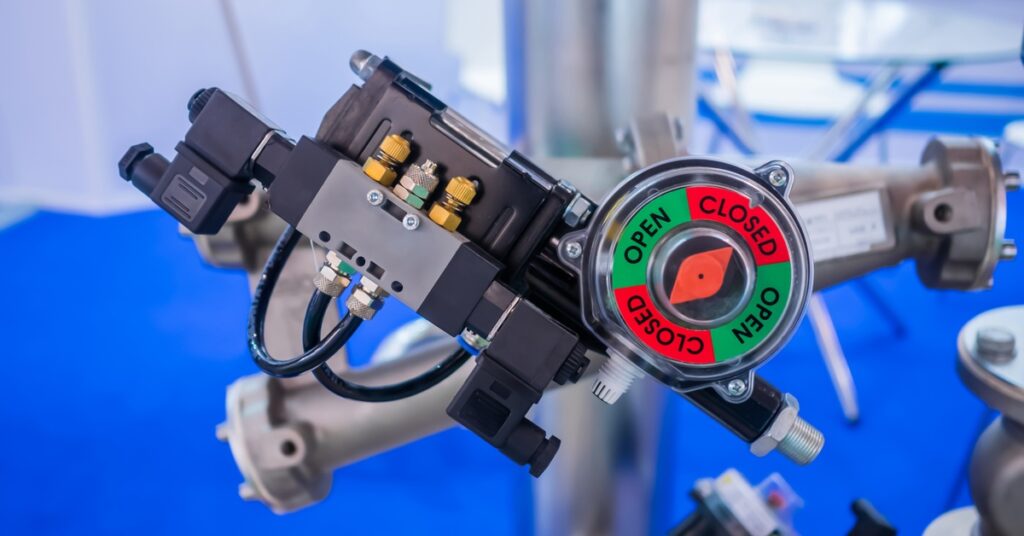
Heating strategies offer another layer of defense when insulation cannot prevent freezing alone. Heat tracing lines applied to inlet tubes or valve housings deliver consistent warming throughout the system envelope. For compact units, cartridge heaters embedded in the valve block or bracket provide targeted thermal energy with minimal power draw.
Sensors embedded near the valve chamber monitor temperature drift and trigger the heating element as needed. In higher-risk zones, full enclosure heating with airflow controls distributes warmth evenly across multiple components. Temperature feedback loops support precision control while extending heater life through regulated duty cycles.
Engineers should size heating systems according to the expected load, ambient conditions, and heat sink properties of nearby metals. Oversized heaters waste energy, while undersized ones allow moisture intrusion and internal frost buildup. Successful heating design requires balancing thermal mass, power supply, and control loop latency.
In applications exposed to prolonged cold without frequent valve actuation, heating elements serve as insurance. Passive insulation only delays freezing, while active heating recovers lost temperature. A hybrid strategy often delivers optimal results where reliability matters most.
Select Materials With Low Thermal Conductivity and Ice-Resistance
Material selection plays a foundational role in freeze mitigation. Diaphragms, seals, and plungers made from EPDM or fluorosilicone resist cracking while maintaining flexibility under freezing pressure. Meanwhile, Polymers like PEEK resist moisture uptake and provide low thermal conductivity, limiting ice formation along surface contact zones.
Engineers should avoid elastomers that harden quickly or fracture under contraction stress. Testing must confirm elasticity and sealing performance at low temperatures under vacuum and pressure. Overlooked material mismatches frequently lead to microleaks, internal vapor traps, or actuation delays.
Low-friction coatings applied to internal sliding parts also help prevent ice adhesion. Dry film lubricants or PTFE coatings help to minimize buildup. Performance advantages compound over time, especially in systems exposed to multiple freeze-thaw transitions daily.
Test for Freeze Resistance Under Simulated Conditions
Testing protocols verify how latching valves perform under pressure, thermal stress, and exposure. Cold chambers replicate real-world conditions to validate design performance and eliminate failure before field deployment. Controlled experiments help refine material combinations, insulation configurations, and heating strategies.
Cycle tests under extreme low temperatures reveal actuation lag, condensation issues, or electrical timing faults. Technicians must measure temperature stability, opening speed, sealing pressure, and response variance.
Every testing profile should match the real operating conditions as closely as possible. Industry standards often miss nuanced risks related to site-specific exposure or seasonal variation. Manufacturers who adapt tests to actual field behavior minimize return rates and build customer trust.
Freeze testing also uncovers integration flaws between the valve and surrounding hardware. Cold shrink, pressure shifts, and bracket flex may not appear under room temperature loads. Proactive validation helps confirm full-system integrity.
At Solenoid Systems, we support OEMs with deep technical expertise and custom solutions that outperform under pressure, temperature, and load. Contact our engineering team to discuss how we can help your platform resist freezing while maintaining precise, reliable actuation.