
Solenoid valves operate with precision, but like any mechanical or electrical device, they can encounter issues. Failures in solenoid valves can interrupt operations, lead to costly repairs, and cause frustration. Thankfully, there are strategies to prevent the common solenoid valve failures, so you can maintain an efficient workflow.
Coil Burnout
Coil burnout occurs when the solenoid’s coil overheats due to prolonged operation or receiving the wrong voltage. Excessive energization for long periods causes heat to build up faster than it can dissipate the heat, resulting in eventual failure.
Another issue involves overvoltage. Electricity flowing through the coil exceeds its capacity and generates excessive heat.
External factors, such as dirt or debris clogging the valve, can increase internal pressure and force the coil to work harder, speeding up its degradation. Workplace conditions—like exposure to high temperatures or lack of proper ventilation—amplify the risk of burnout.
Identifying coil burnout early on helps prevent further damage to the system. Clear signs include a burning smell and visible discoloration around the coil, indicating thermal damage. Technicians can also measure increased resistance in the coil wiring using a multimeter. This higher resistance means internal damage, even with minimal outward signs.
How To Prevent Burnout Issues
Preventing coil burnout starts with ensuring the coil receives voltage that matches its specifications. Always check the voltage rating of the power supply and the solenoid to confirm compatibility. For applications with heavy workloads, install a duty cycle timer to manage the duration of operation and prevent overheating.
Routine valve maintenance—including cleaning internal and external components—reduces friction and clogging that strain the system. When operating in areas with high ambient temperatures, use coils with heat-tolerant materials.
Valve Leakage
Valve leakage is a common solenoid valve failure resulting from worn seals, gaskets, or foreign debris interfering with sealing. Over time, seals wear out naturally due to repeated compression and exposure to fluids and gases. Without regular maintenance, this wear accelerates, weakening the valve’s ability to remain leak-free.
Dirt and particles entering the pipeline exacerbate the problem, sitting on the valve seat and creating gaps. Additionally, system vibrations or misaligned components strain the valve seals, further contributing to leaks. Poor quality construction materials or incorrect sizing make valves susceptible to higher leakage risks.
How To Recognize Leakage Symptoms
If you notice fluid or gas seeping around the valve, it strongly indicates compromised sealing. System pressure fluctuations suggest trouble, especially when performance lags or system outputs don’t meet expectations.
Despite normal operation, a drop in liquid or gas levels may also signal a leakage issue. For example, a refrigeration unit with reduced cooling efficiency may have refrigerant leaks from failing solenoid seals, leading to poor system operation.
Tips for Preventing Leaks
Regularly inspect seals and gaskets for wear and replace them before they completely fail. Use high-quality seals that match the fluids or gases in your system to extend their lifespan. Installing an upstream filter removes debris from the fluid before it reaches the valve, reducing risks from foreign particles.
Ensure the alignment of valve components after repairs or replacements, as misaligned parts can leave unwanted gaps.
Complete maintenance by tightening the fittings. This will prevent additional strain on the seals and maintain a secure connection.
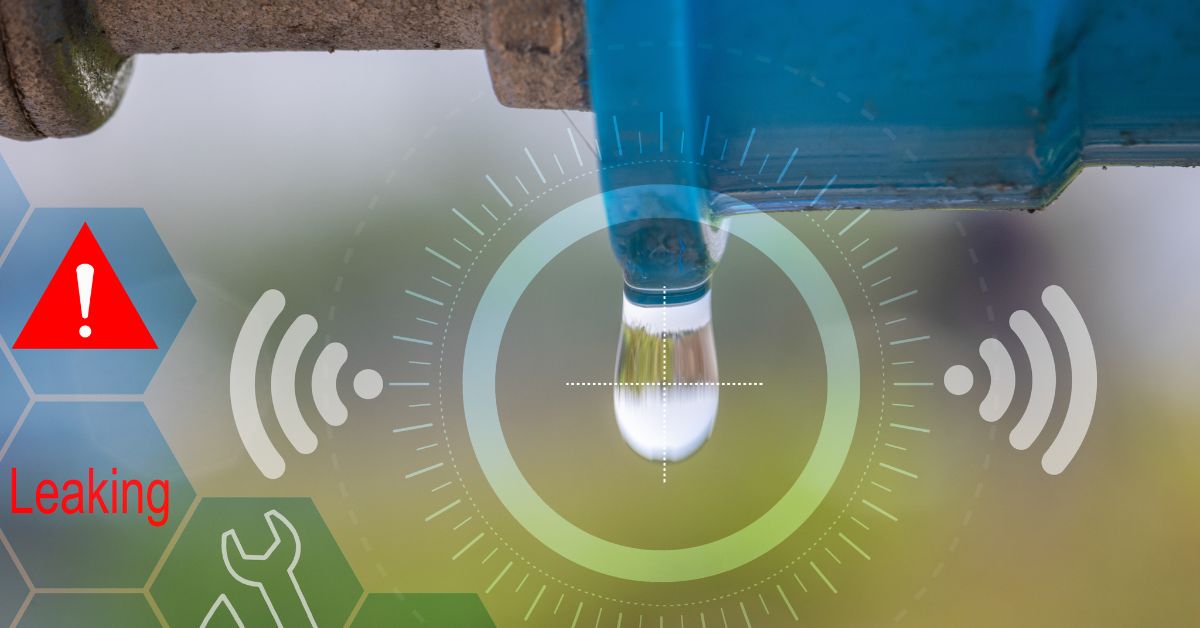
Design Issues
Valves with substandard materials—such as low-grade metals and plastics—tend to wear down faster under pressure or repeated use. Misalignment between the solenoid’s design and the application requirements—like improper size or insufficient pressure handling capabilities—also creates problems.
For example, valves with a narrow flow path can’t manage high-pressure demands, causing flow restrictions or overheating. Poor sealing mechanisms can lead to frequent leaks or inconsistent performance. Even minor design oversights, like inadequate support for temperature fluctuations, drastically affect reliability over time.
Selecting solenoid valves that match system requirements mitigates many design-related failures. Evaluate specifications such as pressure handling capacity, temperature range, material durability, and flow design before making a choice. For example, high-pressure operations may benefit from asolenoid design that incorporates stainless steel or reinforced alloys.
Systems with substantial temperature variations may require valves with thermoplastic components or specialty coatings to resist wear. Partner with reputable manufacturers, like Solenoid Systems, who use advanced technology and rigorous testing to optimize their products.
Stuck or Jammed Valve
A sticking or jammed valve commonly results from accumulated debris, hardened sludge, or mineral deposits forming inside the valve body or around the plunger. This buildup increases gradually in environments with hard water or unfiltered fluids.
Corrosion due to moisture exposure or chemical agents also impairs internal movement and causes stuck components. Poor maintenance practices—like overtightening screws or failing to align movable parts correctly—may add undue stress and hinder smooth operation.
A solenoid stuck in the open position will cause an unchecked flow of liquid or gas, while one stuck closed restricts flow entirely. Sluggish response during operation is another early warning sign, indicating that dirt or deposits are beginning to hinder mobility. Operators may notice resistance or increased force required to move the valve during manual overrides.
Solutions for a Jam-Free Valve
Maintaining a strict cleaning schedule prevents debris from blocking or slowing a solenoid valve. Use quality detergents or solvents to dissolve sludge, scale, and mineral deposits effectively. For valves operating in moisture-prone environments, choose corrosion-resistant materials, such as stainless steel and brass, to maintain functionality longer than standard components.
Ensuring precise torque during assembly or adjustments keeps parts tightly fastened without grinding or binding against one another. Include routine lubrication of movable parts to minimize wear and reduce resistance within the valve.
Excessive Pressure or Overloading
Overpressure occurs when a system applies pressure exceeding the valve’s rated capacity. High-pressure demands exert force on the valve body and internal components, wearing them down at an accelerated rate.
Pressure surges or sudden spikes stress seals, gaskets, and structural parts. These surges occur in systems operating under fluctuating demands, such as brewery pipelines and irrigation systems.
Additionally, valves with incorrect pressure ratings for the application are prone to premature failure due to strain. Overloading components causes loud operational noises, reduced efficiency, and eventual breakdowns. In particular, loud hissing or banging noises point to overloading or pressure surges.
Reduced performance in regulating flow or maintaining pressure stability is dangerous. Damage to external components, including bent and cracked housing, can also indicate the presence of excess pressures.
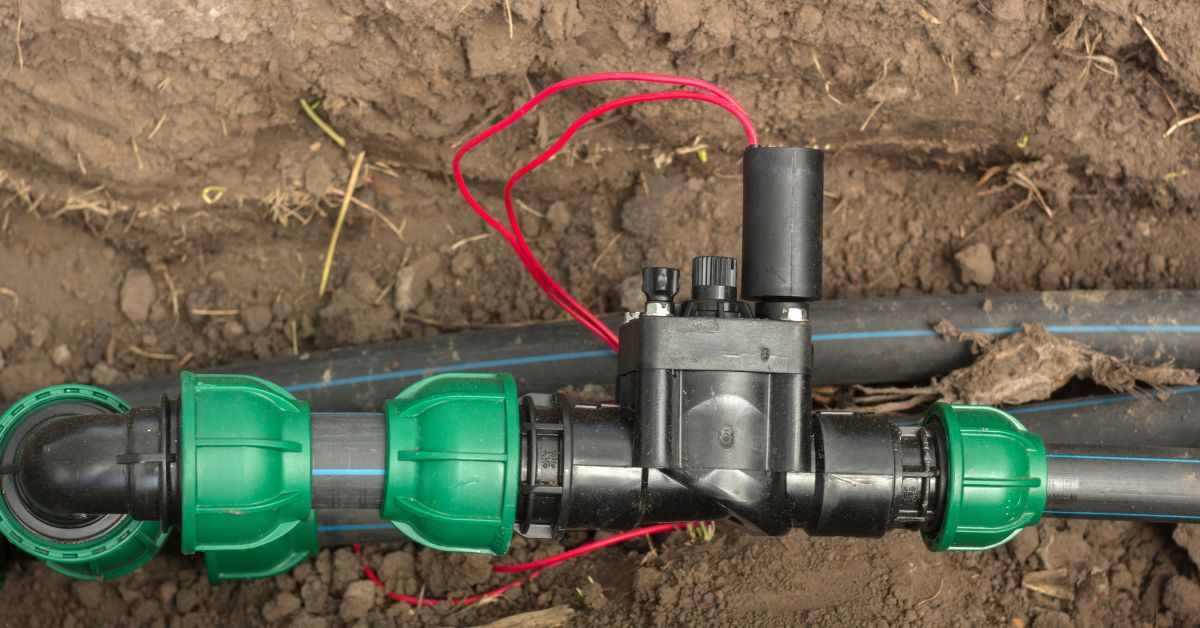
How To Prevent Overpressure and Overloading
Prevention begins with selecting valves that handle pressure levels within your system’s operating range. Confirm that the valves’ maximum operating pressure (MOP) ratings match or exceed the highest pressure the system generates under normal conditions.
Implement upstream pressure regulators or relief valves to limit surges and stabilize system performance. Dampers help reduce the intensity of pressure shocks traveling through pipelines. Perform regular pressure testing and system audits to identify fluctuations and ensure the solenoid valves remain within safe parameters.