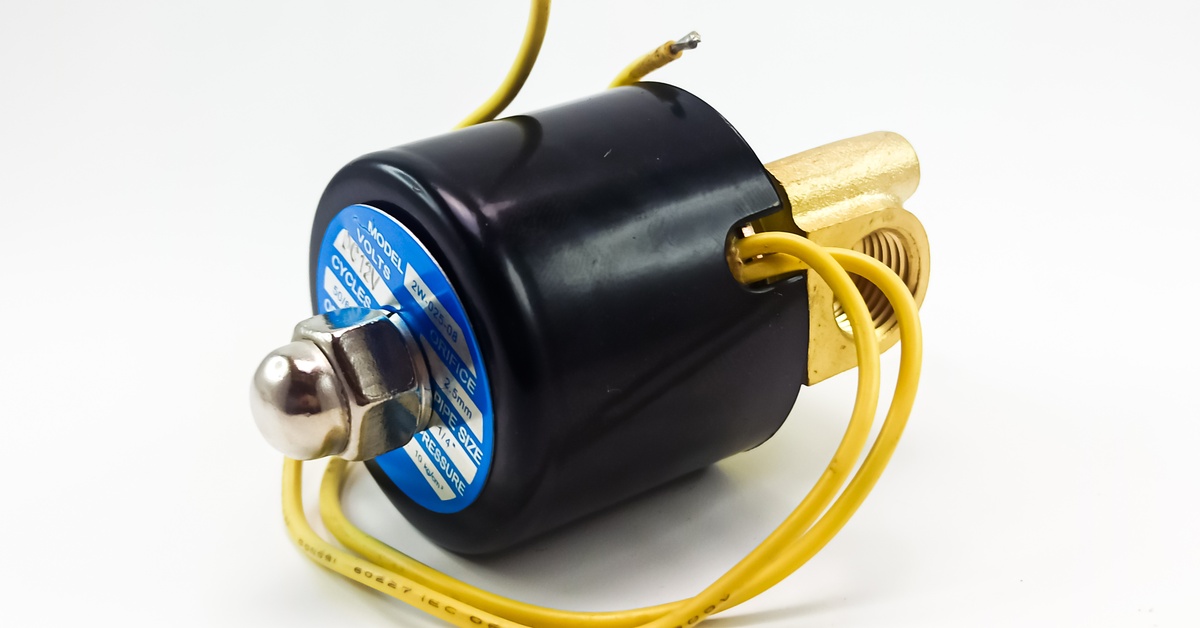
Magnetic latching solenoids redefine how engineers build high-reliability systems requiring precise motion control and minimal power draw. Conventional solenoids rely on continuous current, but magnetic latching models use magnetic fields to retain position after actuation.
System designers in aerospace, medical, and industrial automation environments increasingly depend on this alternative for critical performance gains. Solenoids with latching functionality support stable operation even when energy constraints or thermal limits demand careful resource allocation.
Energy Efficiency and Reduced Heat Generation
Magnetic latching solenoids operate without consuming power between state changes, unlike standard continuous-draw solenoids. That single operational difference dramatically reduces heat buildup within control assemblies. In medical diagnostic equipment, temperature-sensitive components function longer when isolated from heat-generating actuators.
Systems that rely on constant actuation often require dedicated cooling to manage coil temperature and protect surrounding electronics. Magnetic latching designs eliminate that dependency by remaining idle once activated. Automotive platforms, including EV control modules, benefit from both the electrical savings and the tighter thermal envelope.
Power consumption across distributed systems compounds quickly, especially when hundreds of solenoids run simultaneously. Battery-powered instruments, surgical robotics, and portable communication systems extend uptime measurably when using actuators that draw energy only during movement. Engineers seeking greater control over heat and power variables often highlight the advantages of using magnetic latching solenoids in early-stage product reviews.
Manufacturing facilities deploying compact automation cells appreciate the long-term reliability and reduced maintenance schedules enabled by heat-free actuation. Cable harnesses last longer, PCBs endure fewer thermal cycles, and enclosure ventilation needs decline. Each of those factors contributes to leaner builds and longer field service life.
Superior Reliability in High-Vibration Environments
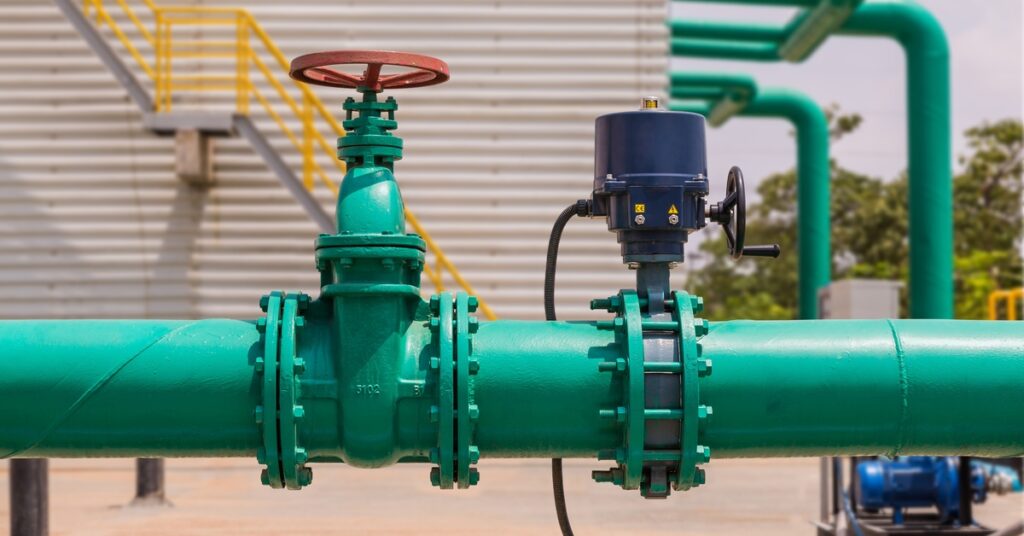
Mechanical vibration degrades standard solenoids by interrupting contact consistency and weakening coil alignment. Magnetic latching solenoids overcome that vulnerability by locking into position magnetically without reliance on sustained power flow. Ruggedized field equipment, such as mobile weapons platforms or drilling rigs, requires that physical certainty.
Vibration resistance allows embedded systems to preserve accuracy without system resets or feedback loop errors. Control units in industrial vehicles or defense infrastructure perform better when solenoids stay firmly latched despite continuous shock or movement. That performance difference reduces false triggers, increases control loop trust, and minimizes diagnostics.
Mounting orientation and shock profiles challenge traditional coils, especially when long-term precision is essential. By contrast, magnetic latching systems maintain engagement during unpredictable terrain movement or high-velocity operation. Platform developers gain confidence in dynamic environments where positional accuracy cannot drift over time.
Solenoids failing under impact disrupt system timing and compromise mission objectives in aerospace, military, and marine applications. Hardware designers often cite advantages of using magnetic latching solenoids when explaining high-cycle performance under mechanical duress. Projects with extreme motion profiles regularly call for this configuration during specification reviews.
Application Flexibility Across Industries
Magnetic latching solenoids fit easily into compact and diverse form factors without imposing thermal or electrical overhead. Portable medical instruments, remote environmental sensors, and robotic end-effectors all benefit from smaller actuators requiring minimal power lines. Design engineers use the freedom to place solenoids in thermally isolated or energy-restricted zones.
Aerospace and defense integrators appreciate that flexibility when retrofitting existing infrastructure or designing modular systems. Solenoids that accommodate spatial constraints and wiring limits provide critical advantages during certification and assembly phases. Compact footprint and cool operation often enable enclosed or shielded configurations with no thermal vents.
Autonomous vehicles—both ground-based and airborne—leverage magnetically latched actuation in valve control, access systems, or feedback-triggered mechanisms. Engineers gain tighter control over payload and voltage distribution across embedded subsystems. With extended uptime and reduced diagnostics, these actuators perform reliably in edge-case deployments.
Solenoid Systems offers engineered actuator solutions to match precise client specifications. Working with a trusted pneumatic solenoid valve manufacturer like us provides direct access to custom coil design, adaptive mounting brackets, and priority production slots. Teams that need rapid prototyping or field-ready configurations rely on our expertise to meet integration demands on tight project timelines.
Fail-Safe Operation and Position Holding
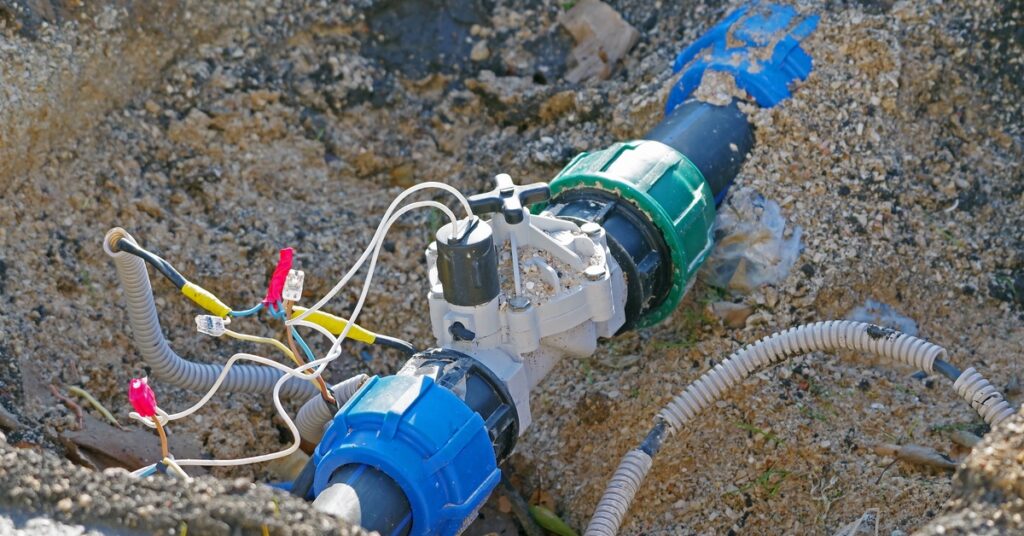
Solenoids that retain their last position when power fails offer crucial advantages in systems with limited redundancy. Magnetic latching designs hold mechanical state indefinitely without current, which prevents drift and unintended actuation during outages. Life-sustaining machinery, fire suppression systems, and flight control modules all require that kind of positional integrity.
Fail-safe performance often ranks higher than speed in mission-critical devices. Unlike spring-return or single-coil solenoids that default to a preset condition, magnetic latching devices preserve the exact system state. That reliability supports consistent restart behavior, reduces false faults, and simplifies reset protocols.
Hospitals, field bases, and aviation platforms cannot afford actuator drift during brownouts or battery changes. Engineers building safety-critical equipment often mandate latching solenoids in final schematics to prevent component failure during contingency scenarios.
Applications where human lives, property damage, or national security depend on actuator stability benefit from magnetically latched solutions. Solenoids in launch control, critical fluid routing, or signal path gating must maintain a state without human intervention. No other configuration offers the same degree of predictable stability during uncontrolled shutdown.
Lower Operating Costs Over Time
Lower energy consumption directly reduces operational costs across multi-solenoid systems deployed at scale. Facilities with hundreds or thousands of actuation points reduce total power draw and HVAC load by switching to magnetic latching variants. Even a 30% reduction in energy per coil scales into major annual savings.
Fewer heating cycles means extended insulation life, delayed coil replacement, and reduced unplanned downtime for component failures. Production managers in continuous-run operations measure downtime in revenue lost per hour, so reliability matters far beyond part cost. Service intervals stretch further apart, and component swap-outs occur less frequently.
Magnetic latching models cut support labor hours by decreasing field diagnostics and system recalibration caused by coil fatigue. Operators in telecom, automation, and medical manufacturing reduce their technician overhead by simplifying solenoid maintenance. Total cost of ownership drops while performance remains consistent.
Cost models accounting for energy, heat mitigation, service time, and coil durability overwhelmingly favor magnetic latching over traditional builds. Lean manufacturing, energy certification compliance, and ESG targets push OEMs to adopt this architecture. Engineers and procurement managers both gain measurable ROI from long-term deployment.
Invest in the Right Solenoids Today
Magnetic latching solenoids serve as high-performance alternatives to conventional solenoids in power-limited, heat-sensitive, or fail-safe-driven systems. Across defense, medical, industrial, and automotive sectors, engineers rely on their efficiency, durability, and reliability to meet complex requirements.
As system constraints tighten and uptime expectations grow, design teams continue to prioritize solutions that deliver maximum function with minimal overhead. Solenoid Systems supports those efforts by delivering custom magnetic actuation solutions designed for critical environments. Partner with us for precision engineering with proven reliability.