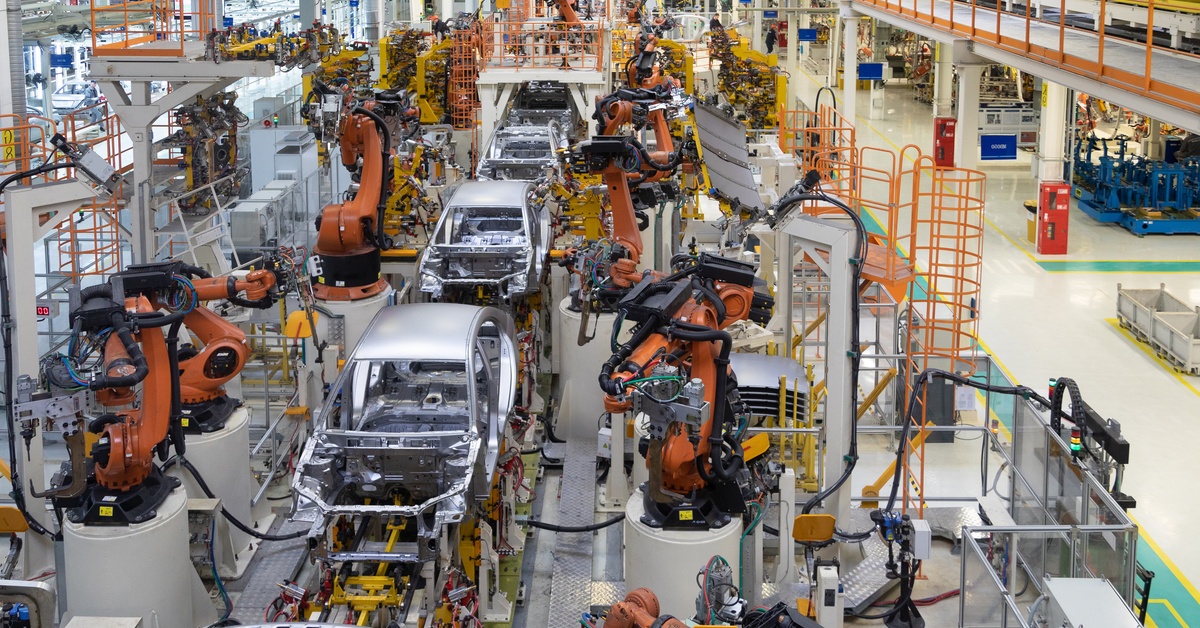
Solenoids have powered automotive progress for decades by translating electrical impulses into mechanical motion. Manufacturers originally relied on basic electromechanical relays to activate systems like starters and ignition switches. Over time, solenoids took on more roles as vehicles demanded faster, more precise actuation.
Engineers recognized their ability to perform under thermal stress, vibration, and load variance. The solenoid now serves as a cornerstone in drivetrain control, emissions compliance, safety systems, and advanced digital platforms.
Early Adoption in Ignition and Starter Systems
Starter solenoids first gave drivers the ability to crank engines with a key rather than a hand crank. Early components delivered mechanical motion by drawing current from the battery to activate the motor drive. Engineers shaped that system around reliability and simplicity, using durable windings and rigid metal plungers.
As automotive production scaled, suppliers upgraded the ignition solenoid to withstand higher cycle demands. Contacts gained better resistance to arcing while casings grew stronger to handle engine-bay conditions. Heat shielding became more critical as engine compartments grew tighter and hotter.
Many manufacturers trace the evolution of solenoids in the automotive industry back to starter motors. Once solenoids replaced foot-operated switches, drivers began expecting electric systems to handle more core vehicle functions. The arrival of electric systems triggered innovation across every major subsystem.
Expansion Into Fuel Delivery and Emission Control
Fuel injection systems introduced high-speed solenoid valves to manage fuel pulses and improve burn efficiency. Precision valves created accurate fuel atomization, which supported better throttle response and reduced consumption. Engineers valued the solenoid’s ability to open and close within milliseconds.
Emission regulations brought purge valves and EGR controls into focus, which relied on vacuum-compatible solenoids. The devices needed chemical resistance, tight leakage control, and rugged mounts. Designers also demanded thermal stability as exhaust-side systems experienced extreme cycling temperatures.
Solenoids replaced diaphragms and cable-based actuators in emission pathways. Response time and cycling lifespan made solenoids ideal for meeting stricter federal requirements. The shift gave engine platforms more tunability while reducing mechanical complexity.
Shift to Transmission Control and Gear Actuation
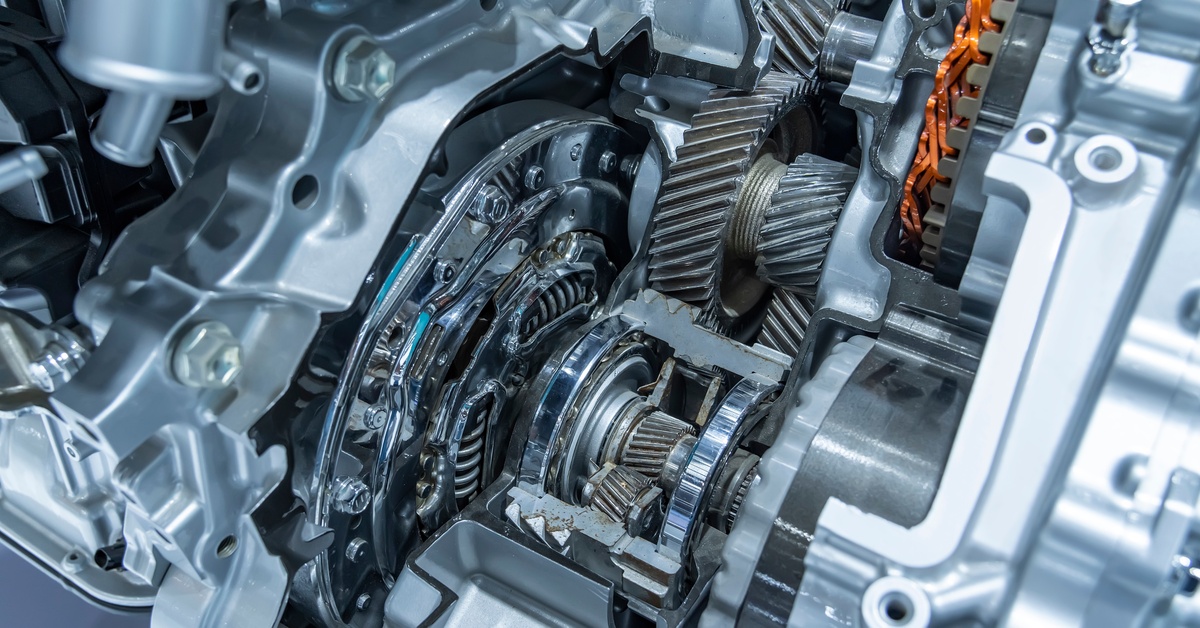
Modern automatic transmissions depend on multi-solenoid banks to control fluid pressure and clutch engagement. Instead of relying on torque converters alone, newer gearboxes use shift solenoids to manage real-time driving dynamics. Each valve contributes to smoother acceleration, deceleration, and grade-based shifting.
Transmission control modules read data from sensors and direct commands to specific solenoids. The modules then signal gear shifts, downshifts, or holding patterns under various conditions. High-flow solenoids allow rapid actuation without compromising pressure precision.
Performance manufacturers commonly request custom stroke lengths or coil windings to match unique fluid characteristics. In high-performance applications, engineers program solenoids to respond differently in sport or economy modes. Adaptive transmissions depend heavily on solenoid behavior to deliver vehicle personality.
Solenoids in Advanced Safety and Brake Systems
Antilock braking systems use solenoids to pulse hydraulic pressure and prevent wheel lock during hard stops. When sensors detect a skid, the controller signals solenoids to release and reapply brake force in milliseconds. Rapid actuation requires high-speed solenoid valves with near-zero failure tolerance.
Electronic stability control expanded solenoid roles into yaw control and lateral force mitigation. Systems read steering angle, wheel speed, and throttle position, then direct solenoids to balance the vehicle. In that role, solenoids indirectly prevent rollovers and improve traction.
Solenoids also appear in emergency braking systems on trucks and commercial fleets. Pneumatic valves with solenoids initiate trailer braking or disengage acceleration during collisions. Safety engineers continue to expand solenoid applications as reliability metrics climb.
Role in HVAC and Cabin Comfort Mechanisms
HVAC actuators rely on solenoids to move blend doors that control airflow across vents. Compact linear solenoids fit into tight dashboards and respond quickly to changes in temperature settings. Quiet operation matters in luxury platforms, so designers choose dampened or insulated casings.
Seat adjustment motors sometimes contain micro-solenoids to lock seat positions or trigger memory functions. Components work with control modules to reproduce exact posture settings for multiple drivers. Memory retention reduces driver fatigue and adds to the perceived vehicle quality.
Window locks and child safety features use solenoids to manage latching mechanisms electronically. Manufacturers choose those solutions over mechanical toggles to save space and improve modularity. Cabin designers push solenoids into more comfort-focused roles every year.
Smart Vehicles and Electronic Integration
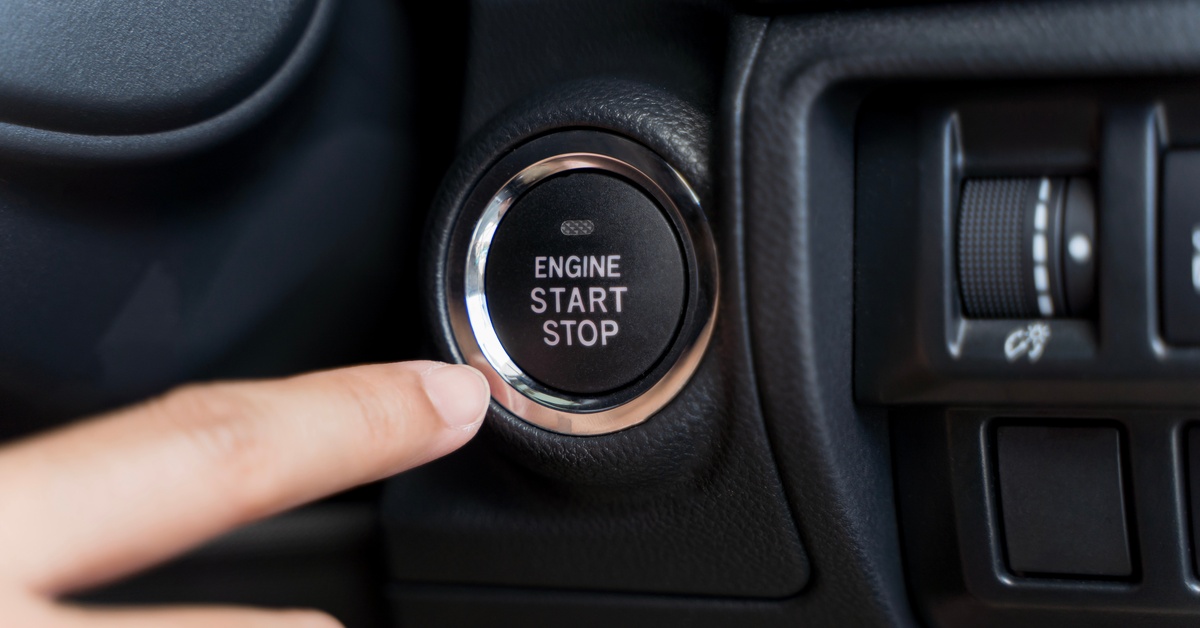
Connected vehicles use solenoids that interact directly with microcontrollers and software-defined platforms. Drive-by-wire systems like throttle control or shift-by-wire rely on solenoids for secure, traceable actuation. Automotive cybersecurity teams now evaluate solenoids for encryption compatibility and firmware support.
Electric vehicles use solenoids in battery cooling systems, contactor control, and charging lockout sequences. Engineers optimize power usage by choosing solenoids with lower holding current or bistable capabilities. Compactness and efficiency become essential at the board level.
At Solenoid Systems, we provide OEMs with application-ready hardware and design support—working with the right pneumatic solenoid valve manufacturers shortens lead times and increases product alignment. Platform-specific tuning and rapid prototyping give clients better control over integration. B2B buyers rely on our expertise to streamline both legacy system upgrades and next-generation launches.
Durability, Customization, and Industry Demands
Tier 1 automotive suppliers demand solenoids that survive hundreds of thousands of cycles under stress. Engineers simulate vibration, salt spray, and thermal spikes to evaluate product durability. Solenoids that survive the trials enter high-volume programs with confidence.
Custom housing geometry helps solenoids fit into tight powertrains, chassis, or interior zones. Offset connectors, unique mounting flanges, and asymmetric coil layouts all reduce space conflict. Solenoid suppliers must respond to automotive packaging constraints without sacrificing reliability.
The evolution of solenoids in the automotive industry now requires programmable, modular, and resilient designs. B2B clients seek suppliers who provide material traceability, documentation, and long-term delivery support. Every component must meet evolving certification standards while adapting to tomorrow’s vehicle platforms.
Stay Ahead With Solenoid Systems
Solenoids continue to shape the future of automotive design with faster response, smarter integration, and greater customization. They started as switchgear but now operate in tandem with cloud systems, sensors, and embedded logic. Manufacturers demand more from each actuator as vehicles grow more complex.
Meeting those needs means understanding how solenoids perform under load, in heat, and within intelligent control frameworks. Reach out to Solenoid Systems if your program demands solenoids that meet both traditional specs and emerging design goals.