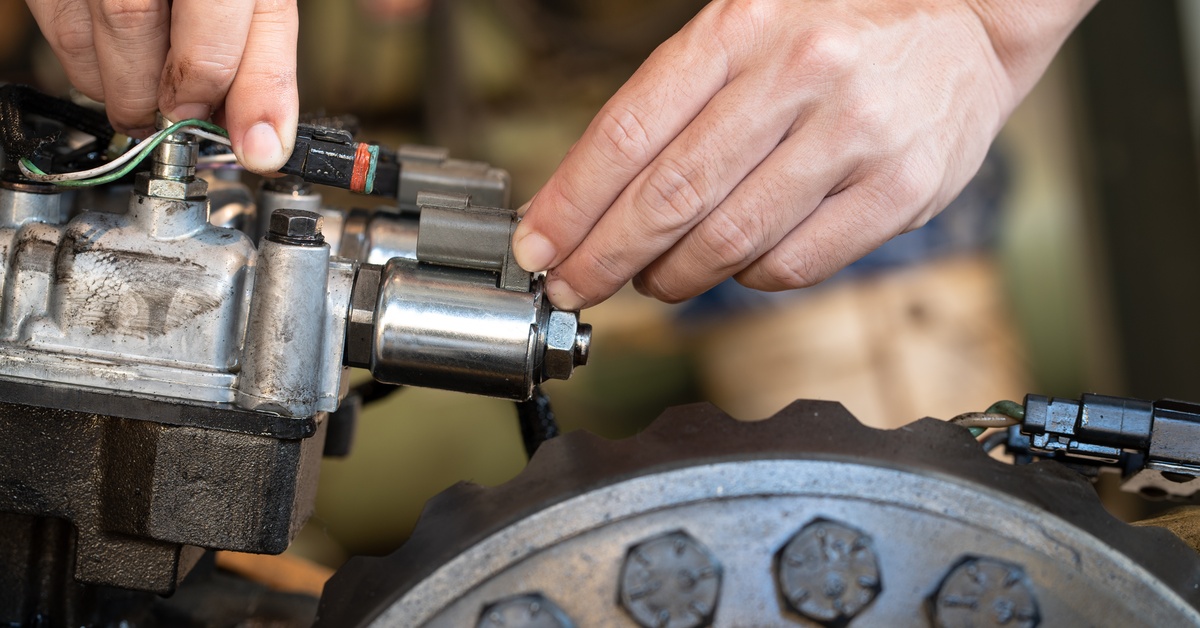
Manufacturers classify solenoids into two types based on the motion they produce: rotary solenoids generate rotational movement, while linear solenoids produce straight-line motion. Both share a similar foundation involving an electromagnetic coil, but they have several differences. Let’s compare key aspects of rotary and linear solenoids, including their functionality, uses, and efficiency.
Functionality and Design
Rotary solenoids rely on electromagnetic energy to produce rotational motion. When an electric current passes through the solenoid’s coil, it generates a magnetic field that interacts with the rotor. Depending on the solenoid’s design, this interaction causes the rotor to rotate partially or fully.
Many models feature specific rotation ranges, from small angles, such as 25 degrees, to complete 360-degree rotations. This flexibility makes them versatile for applications requiring controlled angular movements. They often include return mechanisms, such as mechanical springs or electromechanical systems, that reset the rotor to its original position after deactivation.
Linear solenoids provide straightforward motion by moving a plunger through a coil energized with electricity. The magnetic field pulls or pushes the plunger when the current activates the coil. This motion continues until the current ceases or the plunger reaches its stopping point.
To return the plunger to its neutral state, these devices typically incorporate spring mechanisms that reset the internal components once the circuit breaks.
Key Features of Rotary Solenoids
Rotary solenoids stand out with compact and robust designs that suit devices with limited space. Some models offer unique configurations, such as multi-stroke rotary solenoids, which improve performance in specialized settings. However, their reliance on angular motion limits their versatility compared to other solenoid options.
Key Features of Linear Solenoids
Linear solenoids’ straightforward mechanisms reduce complexity, which enhances their performance in repetitive movements like locking or latching. Besides, their compact design allows for seamless integration into various devices, including printers and fuel injection systems. While they excel in linear motion tasks, their sole focus on push or pull movements limits them from handling rotational tasks.
Applications
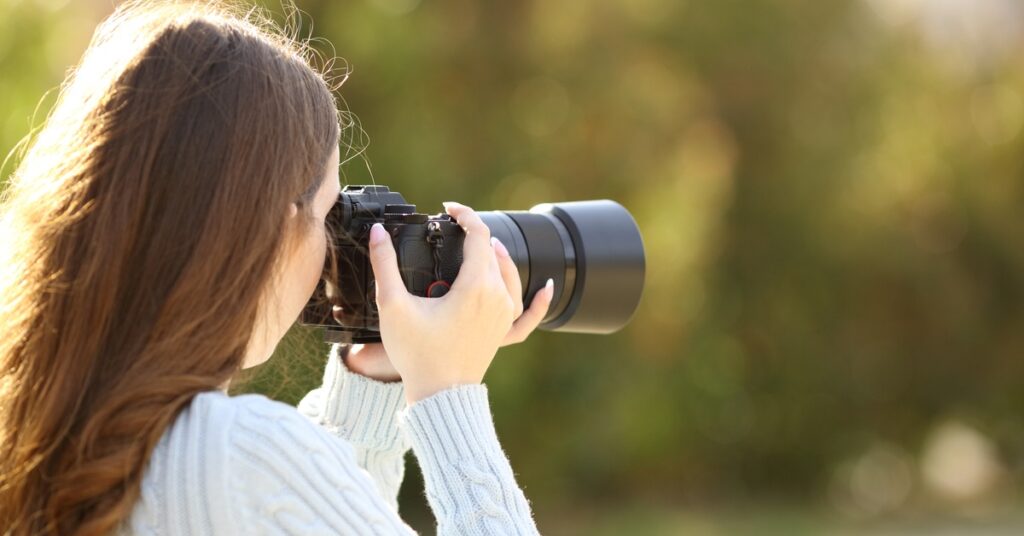
Rotary solenoids excel in industries needing rotational accuracy and controlled motion. Cameras frequently use rotary solenoids for shutter actuation and lens adjustments, improving functionality in high-end photography.
Medical devices also benefit from rotary solenoids’ precision, enabling intricate movements in equipment like lab automation tools or diagnostic machines. Beyond health care, industrial settings take advantage of rotary solenoids for precise valve actuation or flap positioning in automated systems. For example, packaging machinery may use them to position components during assembly or sealing processes.
Linear solenoids fit effortlessly into various everyday devices and industrial machines. Automobiles depend on them for fuel injectors and central locking systems, due to their reliable push-pull motion. Linear solenoids also power essential systems in vending machines, where they dispense products by moving parts in a controlled linear path.
Printers utilize linear solenoids to handle precise paper control, pulling sheets one at a time for accurate alignment. Their simple mechanisms and high load tolerance make them indispensable in heavy-duty applications as well. Water solenoid valves, for instance, integrate linear solenoids to regulate water flow in dishwashers, laundry machines, or irrigation systems.
Performance and Efficiency
When comparing rotary and linear solenoids, assessing performance and efficiency is important. Rotary solenoids deliver exceptional performance in tasks that demand consistent rotational or oscillating motion. Linear solenoids focus on consistent and direct performance in linear actuation tasks. Their simplicity enhances their usability, excelling in scenarios with high force demands, such as automotive systems or industrial machinery.
Regarding efficiency, rotary solenoids outperform many alternatives in angular speed and adjustability. On the other hand, linear solenoids excel in direct, high-force applications, ensuring consistent performance under repetitive stress.
While rotary solenoids might use slightly more energy due to their precision mechanisms, they save time and resources in specialized angular tasks. With their simpler designs, linear solenoids achieve efficiency with lower energy requirements in push-pull applications.
Costs and Maintenance
Rotary solenoids carry higher initial costs because of their compact build and ability to deliver controlled rotational motion, which require advanced manufacturing techniques. Despite the upfront investment, rotary solenoids save costs over time through reliable operations. Their longevity reduces the need for frequent replacements.
Maintenance for Rotary Solenoids
Rotary solenoids maintain performance through proper care and occasional maintenance. Key components like bearings and pivots may wear down over time, especially under heavy operational loads.
Regular inspections can identify early signs of mechanical wear, allowing for adjustments before they impact performance. Lubricating moving parts and verifying the integrity of the return mechanisms can further extend the life of these devices.
Costs of Linear Solenoids
Linear solenoids are less expensive than rotary solenoids. They’re also accessible across various industries, from automated door locks to vending machines. Lower pricing and effective performance allow businesses to scale operations without a high investment. High-load or custom-designed linear solenoids may come with slightly higher price tags, but they remain budget-conscious.
Maintenance for Linear Solenoids
Over time, dirt or debris may accumulate on the plunger, so cleaning this component is essential for uninterrupted function. Heavy-use applications, such as automotive systems or printers, may necessitate occasional replacement of worn-out springs or plungers. Overall, minor upkeep tasks prevent performance dips and extend their operational lifespan.
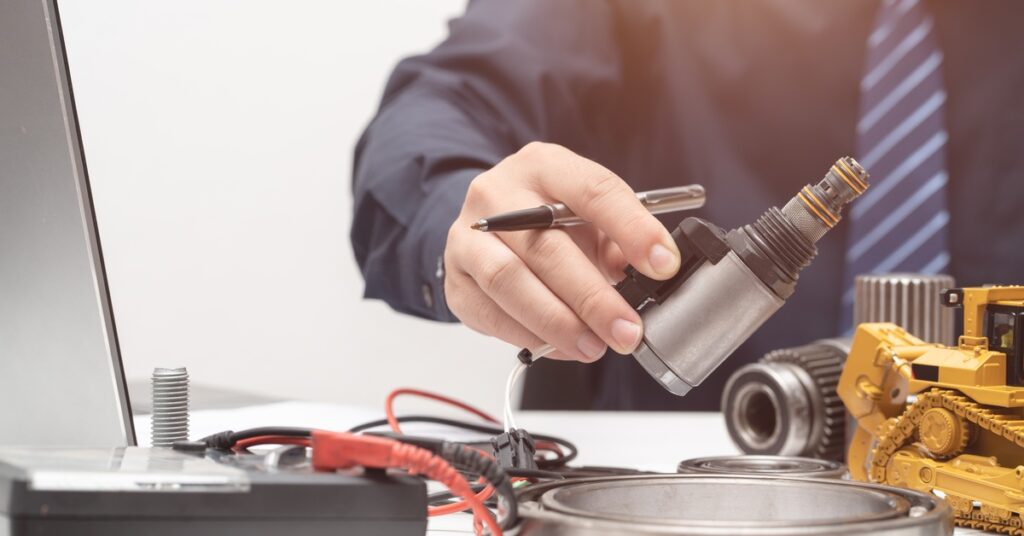
How To Choose the Right Solenoid for Your Needs
Understanding the type of motion your application requires is the first step in selecting the appropriate solenoid. Rotary solenoids provide angular motion, while linear solenoids excel in push-pull actions. Moreover, precision, speed, and force guide the selection process.
Rotary solenoids perform well in specialized environments where you can’t compromise precision, like medical or laboratory equipment. Linear solenoids, however, accommodate tasks demanding consistent force without complex movement paths. Devices such as vending machines or fuel injectors showcase their ability to meet simple, repetitive motion requirements.
Considering Space and Fit
Rotary solenoids fit into devices such as robotics or compact machinery. Their ability to perform intricate movements in small-scale systems makes them indispensable in high-tech environments. Linear solenoids also integrate well into tight spaces, and their simple form provides installation flexibility. However, modifications to meet space restrictions might increase costs or require collaboration with suppliers.
Aligning Application Strengths
Businesses should select rotary solenoids for applications demanding precise movement and advanced control mechanisms. Conversely, linear solenoids make sense for systems prioritizing push-pull actions and simplicity. Overall, both types serve as reliable solutions that become more effective when businesses match them to their intended purposes.
Final Thoughts
Choosing between rotary and linear solenoids comes down to recognizing their distinct capabilities and how they align with your requirements. Each type brings unique strengths, whether it’s the precise rotational motion of rotary solenoids or the straightforward, reliable push-pull action of linear solenoids.
By understanding the functional differences and evaluating your application’s demands, you can make an informed decision that optimizes performance, efficiency, and cost-effectiveness. Ultimately, the right solenoid is one that seamlessly integrates into your system and helps it operate at its best.