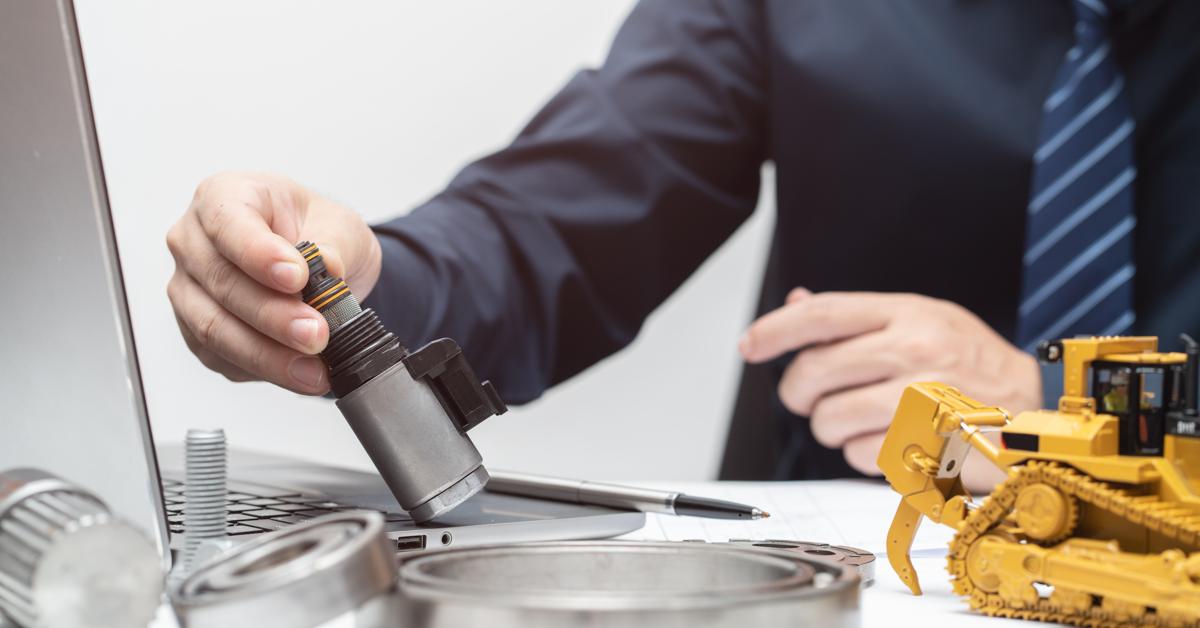
Outsourcing solenoid valve design requires careful planning to avoid issues that could lead to system inefficiencies, equipment damage, or financial losses. In particular, design mistakes can delay operations and impact valve performance. However, recognizing potential problems can help organizations save time and resources. Explore mistakes to avoid when designing solenoid valves and collaborating with manufacturers.
1. Failing To Understand Application Requirements
Every solenoid valve application has unique demands. Skipping a thorough analysis of these needs can lead to poor design choices. For example, a valve for water flow control may fail when it encounters corrosive chemicals unless its materials and internal components can handle such conditions.
Designers should evaluate pressure levels, temperature ranges, response time, and media types before finalizing specifications. A chemical processing facility handling aggressive fluids, for instance, needs valves that can resist corrosion and thermal stress without compromising durability. Collaborating with manufacturers on a detailed checklist can align designs with operational demands.
2. Overlooking the Need for Customization
Standard solenoid valve designs cater to general applications, leaving specialized industries with unmet needs. For example, manufacturing facilities managing adhesives or pharmaceuticals require valves that prevent contamination and withstand specific conditions. Standard products lack the flexibility for such applications, leading to performance and durability issues.
Customized solenoid valves support functionality and integration with specialized systems. Unique coil voltage specifications, specialized seals, or non-standard port configurations allow designers to address application-specific needs. For instance, a chemical processing company handling abrasive or acidic substances benefits from valves with reinforced coatings or resistant materials. These adjustments enhance longevity and reduce the likelihood of downtime due to component failures.
Ignoring Customization Leads to Hidden Costs
Relying on standard solutions eventually increases long-term costs. Mismatched components typically require frequent maintenance or complete replacements, which disrupt operations. For example, a food processing facility requiring valves for hygienic conditions risks compliance issues and contamination when using off-the-shelf products. Engaging with manufacturers who specialize in customizing designs prevents such losses and aligns solutions with operational demands.

3. Selecting the Wrong Materials
Material choice determines how a solenoid valve performs in its environment. For example, valves managing corrosive saline water require stainless steel to prevent failure. Using substandard materials results in premature wear or malfunction under harsh conditions, leading to expensive repairs or replacements.
Determining the Material for the Application
High-temperature systems, such as those in steam generation, demand materials with excellent thermal resistance. Alloy valves ensure safe and efficient operations. Conversely, medical devices requiring biocompatibility rely on FDA-approved materials for patient safety. Identifying media types, operating pressures, and temperatures helps to avoid improper material selection while ensuring compliance with manufacturing standards.
Manufacturer Expertise Makes a Difference
Partnering with a manufacturer experienced in various industries simplifies material selection. These partners evaluate applications closely, recommending durable and efficient materials without compromising quality.
Technical consultations can also explore options for coatings or internal component upgrades to improve valve performance under extreme conditions. With their expertise, business leaders can make informed material decisions.
4. Overlooking Compatibility With Existing Systems
Overlooking compatibility with existing systems is a big mistake to avoid when designing solenoid valves. Valves must align with power supplies, mounting configurations, and other system elements to function efficiently. Physical mismatches, like differing pipe sizes or mounting adapters, require costly modifications.
Electrical mistakes, such as using a valve for alternating current on a direct current control panel, can cause system failures and delays. Businesses that neglect these factors risk inefficiencies, including inconsistent valve cycling and production setbacks. For example, a pharmaceutical company expecting seamless integration may face delays if connectors or input requirements don’t match their systems. By sharing detailed schematics and operational parameters with manufacturers, the valves will align with a business’s systems.
5. Ignoring Environmental Factors
Industrial environments impose various stresses on solenoid valves. Components facing harsh external conditions, such as extreme heat, freezing temperatures, or corrosive environments, face high risks of malfunction.
For instance, valves in arid climates may crack or warp if they lack materials that resist thermal expansion. Similarly, systems handling dusty or particle-laden air require valves with enhanced sealing to avoid operational inefficiency. Ignoring environmental nuances leads to equipment failures that disrupt production.
Custom valve designs address specific environmental threats more effectively than standard models. Manufacturers can fine-tune every detail, from the lining material to flow rate precision, so the product withstands harsh operating environments.
6. Skipping Testing and Validation
Tests provide insight into how solenoid valves perform under varying conditions, eliminating uncertainty before deployment. Without validation, business leaders risk installing components that fail under pressure or wear out prematurely.
Testing covers thermal tolerance, pressure resistance, and chemical durability to mimic real conditions. For example, water treatment plants handling corrosive fluids benefit from immersion and exposure tests that evaluate how materials react over time.
Engaging with manufacturers with testing standards streamlines the validation process. Reliable partners incorporate advanced evaluation methods and simulations to ensure valve performance meets operational benchmarks.
Manufacturers specializing in proportional solenoid valve design, for instance, apply specialized tests to guarantee precision and resilience. Investing in quality validation saves resources and time and builds trust in long-term operational integrity.
7. Falling for the “Lowest Cost” Trap
Attempting to reduce upfront expenses by choosing low-cost solenoid valves results in financial burdens. Components with inferior materials or featuring weaker seals may fail prematurely in demanding applications.
For example, valves with budget-grade seals tend to rupture under high-pressure fluctuations in gas pipelines, leading to leaks, repairs, or operational shutdowns. Business leaders who prioritize low prices over high quality risk frequent failures.
Well-manufactured solenoid valves offer consistent and reliable performance, which translates to fewer breakdowns and reduced maintenance expenses. Working with dependable manufacturers prevents low-cost traps. Reputable companies guide clients through material selection, technical specifications, and testing so that the product meets the needs of the application.
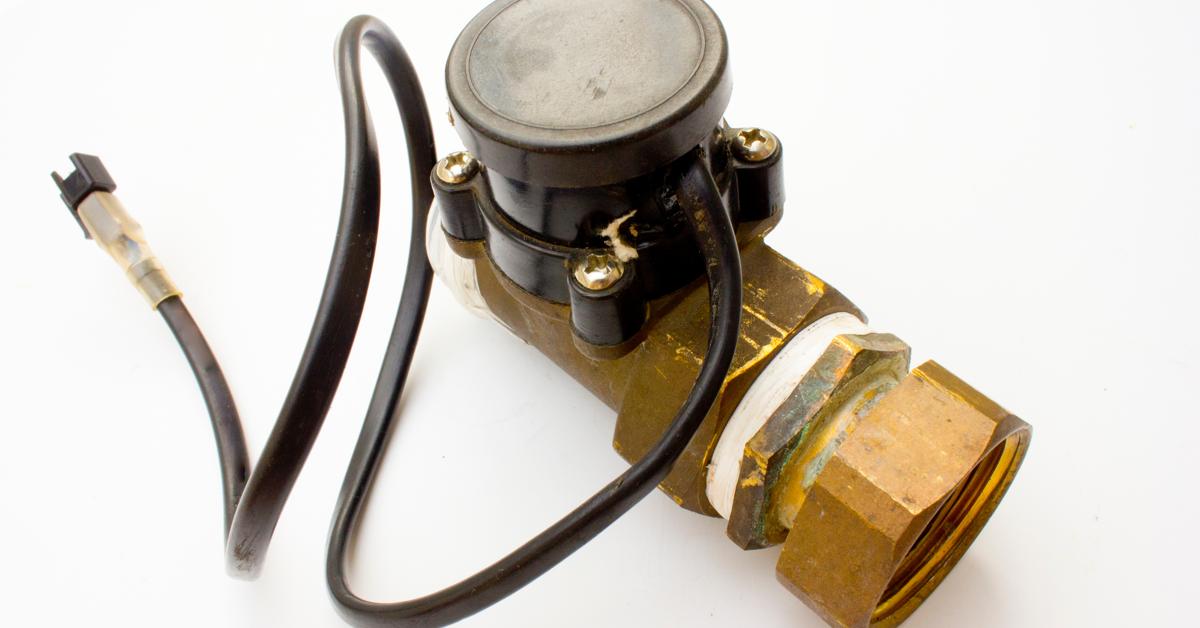
8. Choosing the Wrong Solenoid Valve Manufacturer
The products and services of solenoid valve manufacturers differ in quality. Some offer basic designs that lack customization for overcoming industry-specific challenges. Others specialize in custom solutions that meet complex industrial needs. Choosing a poorly rated manufacturer leads to delayed timelines, inadequate components, or substandard materials that fail prematurely.
At Solenoid Systems, we deliver precision-engineered, durable solenoid valves that meet the demands of your application. We collaborate with our clients from concept to execution, guaranteeing timely project completion. Choosing Solenoid Systems is a partnership rooted in excellence and trust.