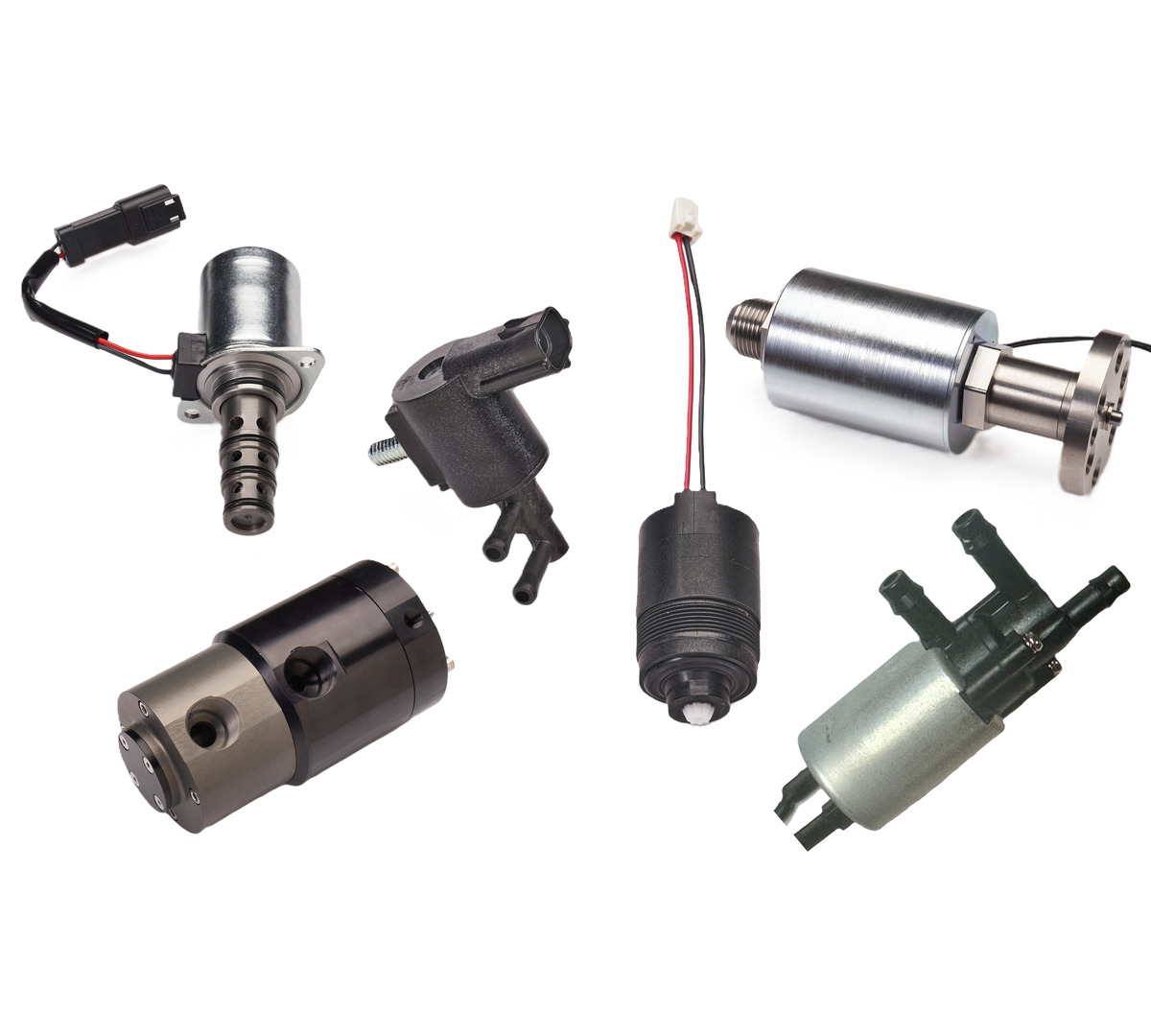
Understanding the differences between direct-acting and pilot-operated solenoid valves simplifies decision-making for industrial applications. Solenoid valves, crucial in controlling fluid flow, depend on electromagnetic principles for operation. Choosing the right type involves evaluating performance factors, specific needs, and application environments. This comparison sheds light on these two types, helping you make informed choices.
Understanding Solenoid Valves
Solenoid valves are essential components in various industries, from manufacturing to water treatment. They control the flow of liquids or gases using an electromagnetic solenoid coil. When energized, this coil generates a magnetic field that actuates the valve, enabling or restricting flow. Key parts include the solenoid coil, plunger, and valve body. Industries employ these valves for their reliability and efficiency in applications such as automated control systems and safety interlocks.
Direct-Acting Solenoid Valves
Direct-acting solenoid valves are known for their quick response times. The solenoid coil directly moves the plunger, offering immediate control over fluid flow. This simplicity ensures fast and reliable operation, perfect for systems demanding rapid switching.
While these valves suit low and high-pressure environments, they manage lower flow rates and consume more energy than pilot-operated valves. Common applications include water and airflow management, where performance consistency matters.
Working Principles of Direct-Acting Valves
These valves operate using direct electromagnetic force. Energizing the coil pulls the plunger, opening or closing the valve without external pressure. This straightforward mechanism equates to fewer moving parts, enhancing durability and reducing maintenance. Such simplicity benefits applications requiring reliability and minimal downtime.
How Do They Work in Their Common Applications?
Understanding how direct-acting solenoid valves operate in various applications optimizes system performance and ensures reliability. As mentioned, their unique design offers rapid response and precise control. Here are their common applications and the operational advantages they provide:
- Water flow control in dispensers. Direct-acting solenoid valves manage water flow in dispensers by quickly starting or stopping the flow. This rapid action prevents spills and maintains precise measurements, providing a reliable and user-friendly experience.
- Air control in pneumatic systems. These valves offer fast switching capabilities in pneumatic systems, necessary for controlling airflow in automated processes. Their direct operation eliminates delays, which is vital for applications requiring precise timing and coordination. They function without auxiliary pressure, simplifying system design and reducing failure risks.
- Fuel systems in automotives. In automotive applications, direct-acting solenoid valves control fuel injection systems. They operate under varying pressure conditions, improving engine efficiency and reducing emissions.
- Medical equipment. Medical devices such as ventilators and dialysis machines rely on the precision and reliability of direct-acting solenoid valves. Their straightforward mechanism maintains consistent operation. The compact valve design allows for easy integration into complex medical systems.
Pilot-Operated Solenoid Valves
Pilot-operated valves can handle larger flow rates, leveraging line pressure for actuation. A pilot valve controls the main valve, requiring a minimum pressure differential. These valves consume less energy but respond slower than direct-acting valves. Ideal for scenarios involving large fluid volumes, pilot valves support long-term, high-volume operations like irrigation or extensive pipeline networks.
Design and Mechanism of Pilot-Operated Valves
Pilot-operated designs integrate a smaller pilot valve to modulate the main valve’s position. Line pressure aids in opening and closing processes, conserving energy. Though unsuitable for low-pressure scenarios, this design controls substantial fluid flows, balancing performance and energy use.
How Do They Work in Their Common Applications?
Knowing how pilot-operated solenoid valves function in their common applications maximizes efficiency and reliability in large-scale fluid management systems. Their design leverages line pressure to control substantial flow rates, making them indispensable in many industrial settings. Let’s explore their typical applications and the unique advantages they offer:
- Irrigation systems. Pilot-operated solenoid valves manage large volumes of water in irrigation systems. By utilizing line pressure, they open and close main valves, conserving energy while handling extensive operations. Their design supports the delivery of water across agricultural fields.
- Pipeline networks. These valves control fluid flow in extensive pipeline networks. They manage large fluid volumes by leveraging existing pressure, ideal for long pipelines where maintaining flow consistency is essential. Their energy-efficient operation and ability to sustain high-volume throughput make them vital for transporting oil, gas, or water over long distances.
- Industrial process control. Pilot-operated solenoid valves regulate the flow of gases and liquids in manufacturing systems, using line pressure to maintain accuracy and efficiency. Although their response time is slower compared to direct-acting valves, they provide stable and reliable process control.
- Water treatment facilities. The valves manage the flow of water through various treatment stages. Their capability to handle large volumes while conserving energy benefits large-scale facilities that demand continuous operation.
Comparing Direct-Acting and Pilot-Operated Solenoid Valves
The difference between direct-acting and pilot-operated solenoid valves lies in their unique strengths. Direct-acting valves deliver rapid response times, making them perfect for tasks that demand quick operation and handle lower volumes.
On the other hand, pilot-operated valves conserve energy, ideal for scenarios where managing large volumes with minimal energy is important. When deciding between them, consider the demands of your applications.
For example, in a car wash system, where quick and precise control of water and cleaning solutions is necessary, direct-acting solenoid valves are ideal. This is because of their fast response times and ability to handle lower flow rates so that each vehicle receives the right amount of cleaning solution without delay.
In contrast, pilot-operated solenoid valves would suit a municipal water supply system that requires the management of large volumes of water over long distances.
Integration of Proportional Solenoids
What’s something direct-acting and pilot-operated solenoid valves have in common? Both solenoids can integrate with proportional solenoids, providing a shared advantage in control precision. This integration allows for variable valve positioning for precise adjustments to flow rates.
Such precision supports applications like chemical dosing and advanced manufacturing, where accurate control is paramount. By fine-tuning flow rates, systems achieve optimal performance with less waste. This enhanced control leads to better outcomes in demanding environments.
Conclusion
At Solenoid Systems, we understand the critical role of selecting the right solenoid valve in optimizing your industrial operations. Whether you need a direct-acting valve’s rapid response or a pilot-operated valve’s energy efficiency, our team is here to guide you through the decision-making process.
We take the time to understand your unique operational needs and can craft custom solutions just for you. Our expertise ensures you achieve efficient and reliable fluid control that aligns with your specific requirements. Contact us today at (262)-622-6564 for more information. We look forward to working with you!